Integrating a DPTE® transfer system to the Flow Sciences, Inc. Glovebox Workstation
Allan Goodman, Ph.D., Lab Manager;
Stephen Janz, VP International Sales & Business Development
Background
A client’s containment application required a method to provide containment of highly cytotoxic compounds throughout a process of weighing, dispensing and sample transport. A Flow Sciences Glovebox Workstation enclosure would provide process containment, however effective sample transport containment between laboratory locations was needed.
The Challenge
The client needed an “interim containment” solution for the process which involved powders classified as Highly Potent Active Pharmaceutical Ingredients (HPAPI). This required a leak free interface between the Glovebox Workstation and the containment device which would be utilized for sample transport between two enclosure locations. Client safety policy stipulated that the operator’s respiratory exposure concentration, or Occupational Exposure Limit (OEL) expressed as an 8-hour Time Weighted Average(TWA), would be less than 500 nanograms per cubic meter air (<500 ng/m3). Some clients express this as a Containment Performance Target (CPT) for the enclosure or process of <500 ng/m3 per 8 Hour TWA.
The Solution
Flow Sciences designed the enclosure utilizing a Getinge DPTE® Alpha Rapid Transfer Port (RTP) to enable contained sample transport. This solution built upon Getinge DPTE® Beta Containers (DPTE® PE Container) already in use at the facility. The Beta containers were being used for safe leak-tight transfer of cytotoxic products from one contained work area to another. To maximize the functionality of existing, validated re- sources, the Flow Sciences enclosure used a Getinge DPTE® Alpha port fit with the DPTE® Beta containers.
The negative-pressure enclosure provided personnel and product protection through HEPA Filtration and four (4) 10” oval glove ports on the front of the unit. Specifically, “personnel protection” entails employee protection from respiratory or dermal exposure. The Glovebox Workstation is a ‘closed’ system comprised of a polypropylene superstructure, integrated gloves and HEPA filtered air into and out of the enclosure. The 99.99% efficient inlet HEPA filter combined with the bag-in/bag-out dual HEPA exhaust fan-filter unit allows smooth airflow into and through the enclosure, while providing an interior cleanliness level of ISO Class 5 or better.
The Solution in Action
After product is weighed, it is containerized for transport. An inherent exposure hazard still exists in the event of a catastrophic spill event during transport. Secondary containment during product transport is provided by the DPTE® Beta containers, thereby serving as an engineering control for this hazard.
By incorporating a DPTE® Alpha port on the side of the enclosure, the process is enabled to securely transfer weighed, containerized HPAPI product directly into the Beta Container by performing the following steps in chronological order:
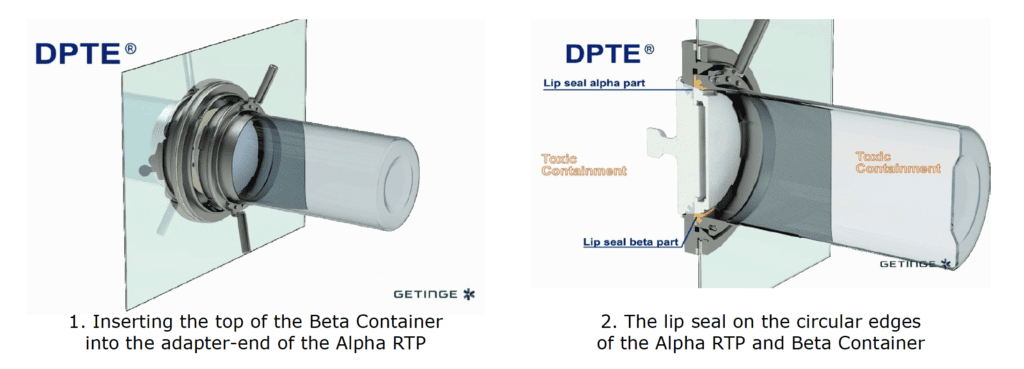
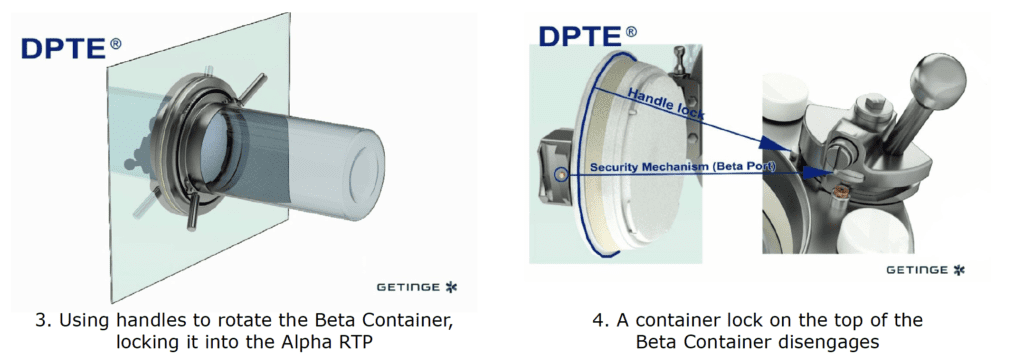
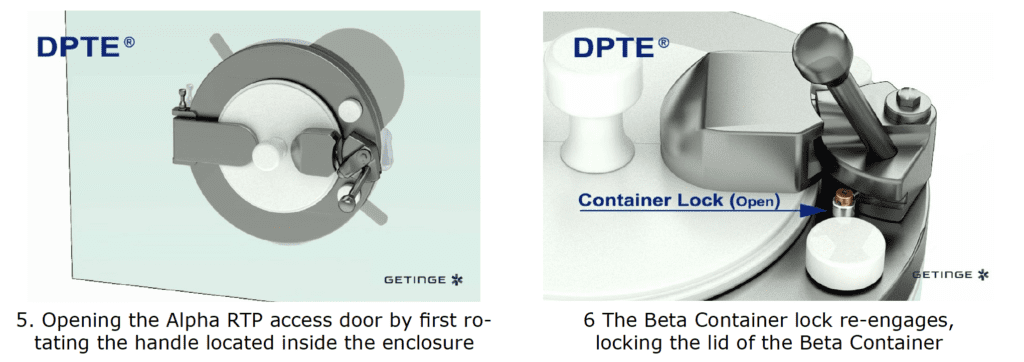
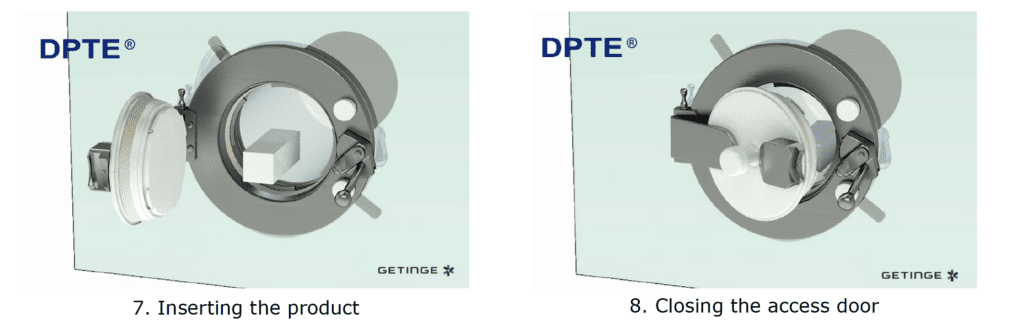
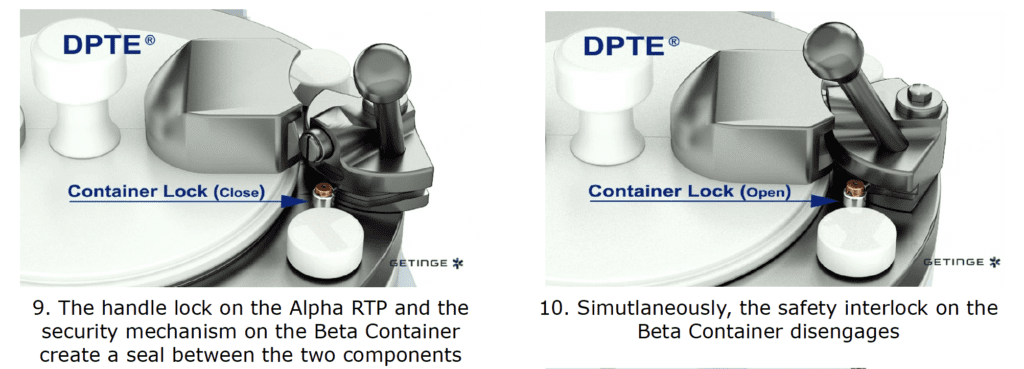
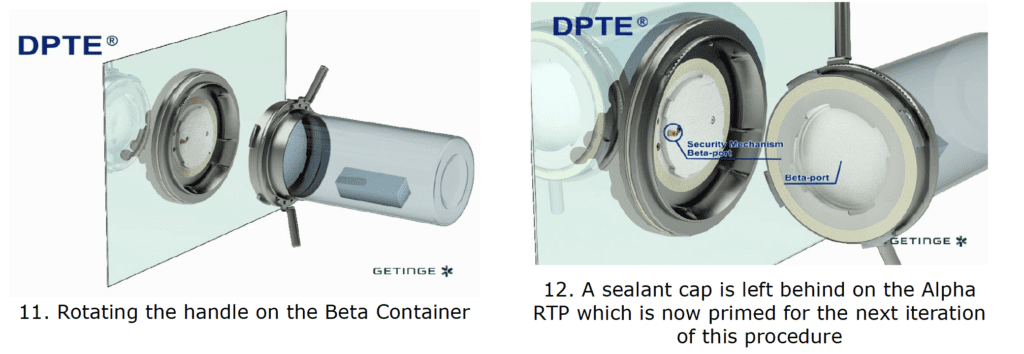
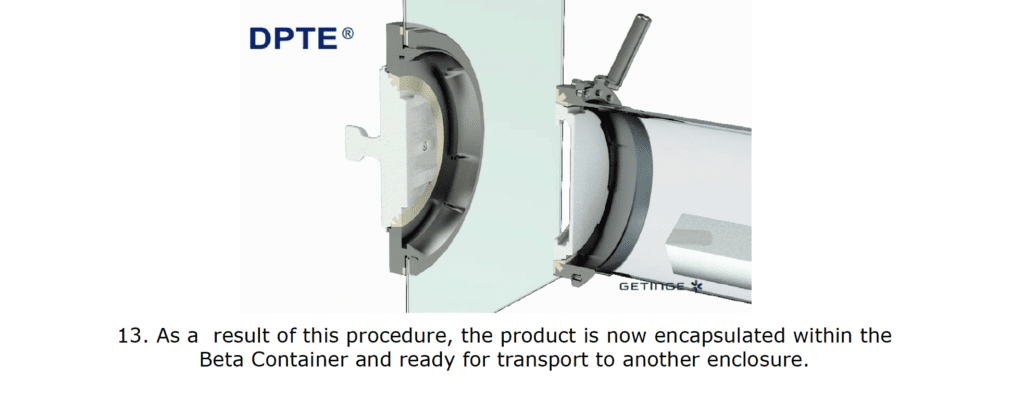
The Result
The Flow Sciences Glovebox Workstation contains toxic powder substances and the operations that involve them, to levels well below the Occupational Exposure Limit (OEL) stipulated by the customer (<500 ng/m3). Exposure risk during transfer and transport of the product between different locations was controlled by the leak-tight DPTE® container system integrated into the client’s weigh, dispense and sample transport process.
Ray Ryan, President and CEO states “Flow Sciences is a solution-based company. Sometimes we have the solution on our shelves, but most of the time we have to develop a solution to fulfill that industry need”.
This case study serves as an example of a project where Flow Sciences used a recognized transport solution in conjunction with our proven containment systems to fit the specific needs of the client.