The primary mission of Flow Sciences is to contain hazardous materials. We maintain a laboratory for containment performance verification, relevant standard testing, and product development.
We test every unique enclosure that is manufactured for reliable performance.
Merck has chosen many times with us to verify containment performance further through surrogate powder testing. Recently we have hosted Merck at our facility to complete surrogate powder containment validation on an Analytical Process Isolator, as well as a blending and dispensing containment system.
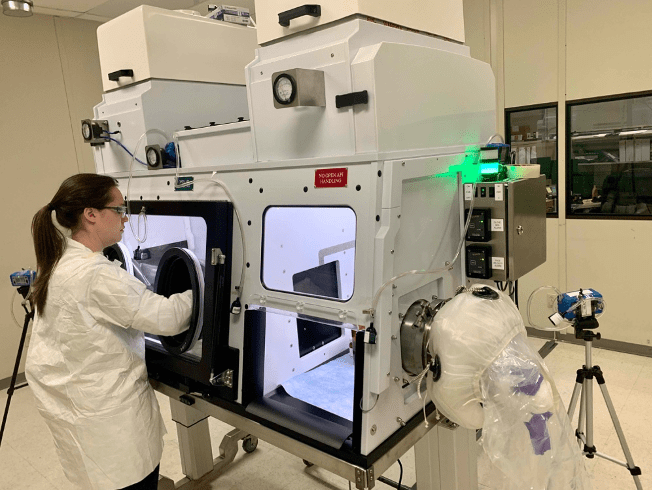
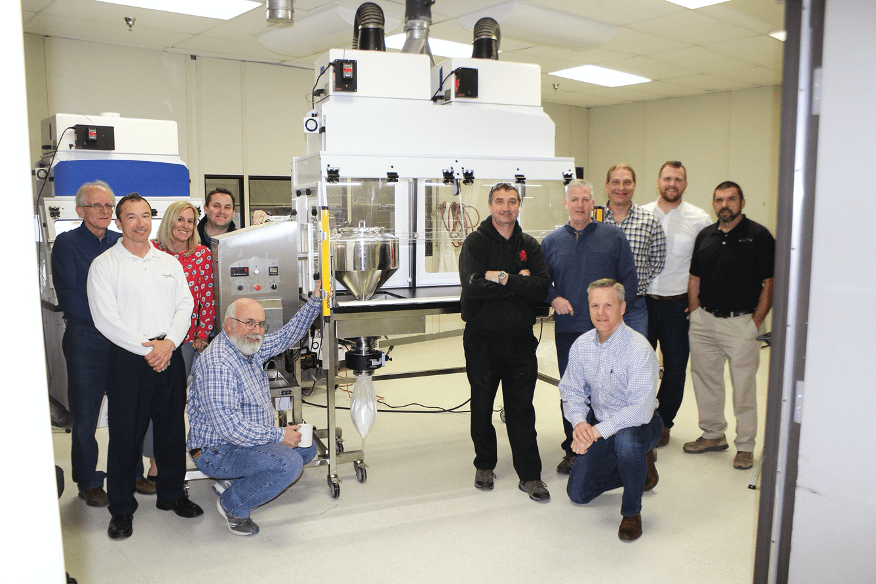
Once a final design has been decided upon, the unit is manufactured and the containment performance of the engineering control is verified and validated to the essential standards.
It is sometimes desirable/necessary to perform surrogate powder testing to further evaluate enclosure performance using simulated operations. This includes an imitation of the application in our laboratory at FSI headquarters in Southeast North Carolina.
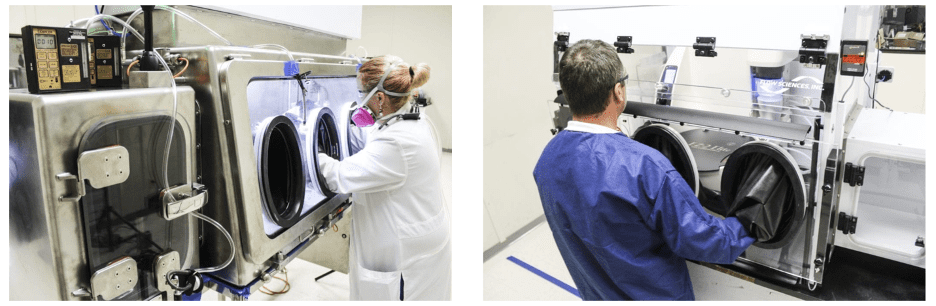
Often, we have customers and third-party Industrial Hygienists come to the facility and mimic the task they will be completing in their lab. This allows for the actual end users and operators to perform the SOP and test for things like ergonomics and workflow.
If you dispensing highly potent and toxic powders into a charge bag for example, you may want to practice a few times to make sure you’re successful and safe. This is where FATs (Factory Acceptance Testing), SPT (Surrogate Powder Testing), and SCP (Safety and Containment Program) planning are so critical to improving your odds of success.
We have been fortunate enough over the years to make great connections with industrial hygiene companies around the world that partner with us to perform SAT or FAT. Companies such as ISS, IES, Safebridge, and others often monitor the testing or run their own samples for third-party validation.
Testing aside, at FSI we also aide in the development of good lab practices and proper SOP during the application. Moreover, we can provide cleaning protocols to guide decontamination and proper cleaning to prevent containment breaches and cross contamination.
The standard testing, however, can be seen in the graphic below.
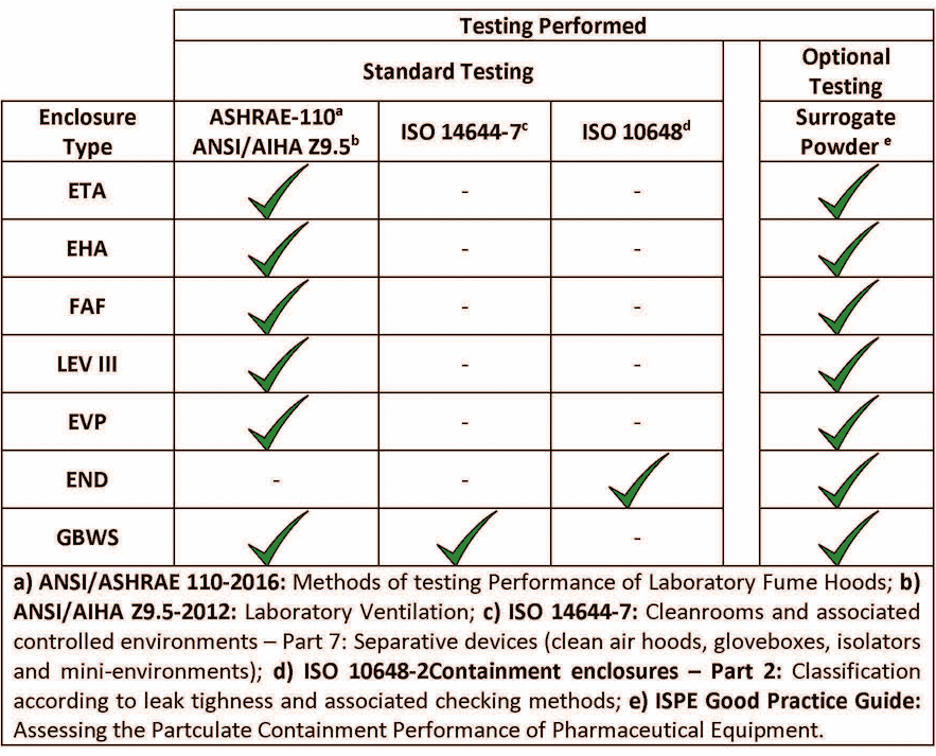
ASHRAE 110-2016 compliance testing is the standard for most fume hoods and powder containment enclosures. If the CPT (containment performance target) is below the limit of detection of the ASHRAE test, more testing is needed for accurate containment data.
In ASHRAE 110-2016, the hood will pass at anything below .05 ppm, or 292 μg/m3. If the required OEL (Occupational Exposure Limit) is .1 μg/m3 or 100 ng/m3, that is much lower than the acceptable pass exposure for ASHRAE 110-2016. You can see in the graphic below, surrogate powder testing is needed below the ASHRAE limit of 292,000 nanograms.

Engineering controls are only one part of a comprehensive strategy for containment. A surrogate powder FAT and SAT, that includes Good Lab Practices and SOPs, defines how the end user will interact with the process. This provides for the most reliable indication of expected performance. Compliance with solid SOPs and training combined with an ongoing sampling plan can help sustain consistent containment results.
We look forward to working with you to not only design a containment solution, but also ensure that it will contain the entire process and train operators on how to properly use the engineering control to mitigate exposure and ensure process integrity.