
Abstract:
As active pharmaceutical ingredients increase in potency and become more hazardous to work with, pharmacological and chemical containment devices are required to meet containment performance targets through independent testing before use in laboratories can begin. Typically, we test containment equipment against some minimum performance standard. This is necessary to protect procedural integrity and the sensitive products undergoing processing.
As air sampling and measurement techniques improve and cumulative recorded data becomes more robust, containment testing has grown more refined—even if the tests themselves are more complicated.
There are many reasons why such changes have occurred and influenced the design and production of containment units and the means of evaluating them. Powders and liquids are dangerous to handle over long periods, and the manipulating process equipment is more substantial in both size and capability. Testing is not one-size-fits-all when it comes to containment performance—here we will analyze and explain the different methods, their reasons, and which would be most beneficial for your first (or next) containment device to ensure personnel protection.
Discussion:
Over the last century, the use of devices designed to contain toxic gases, volatile liquids, and powdered solids has grown substantially within most operating labs and pharmaceutical production facilities.
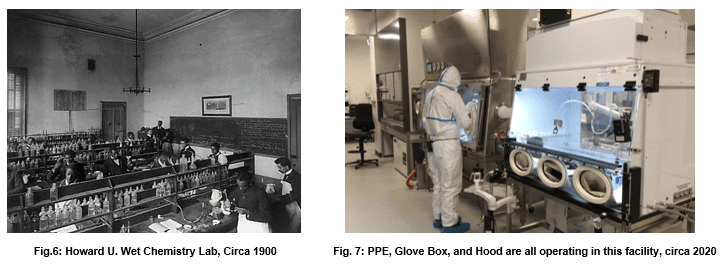
The writer has previously examined this issue1. The following table represents current containment standards used worldwide to evaluate various lab and powder containment equipment in multiple contexts:
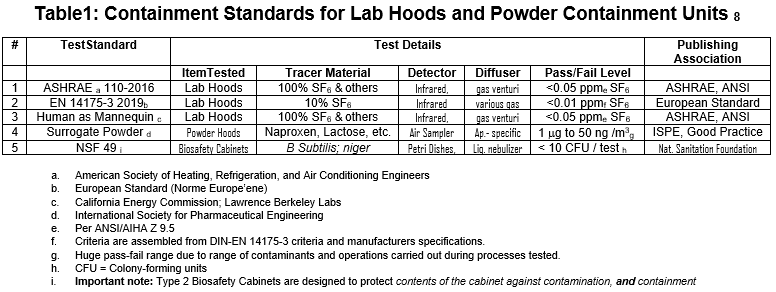
ANSI/ASHRAE 110-2016
ASHRAE 110 clearly states the standard’s scope in Section 1. Purpose: “The purpose of this standard is to specify a quantitative and qualitative test method for evaluating fume containment of laboratory fume hoods.” In North America, ANSI/ASHRAE 110-2016 is the most frequently used fume hood containment test 5.
Since 1985 when this limited scope was crafted, application of the 110 test has steadily expanded from lab fume hoods to other types of exhaust ventilation units including small worktop units, 100% exhausted biosafety cabinets, and even filtered ductless units.
In the latter case, the filtered exhaust air must not re-enter the test area when expelled from the unit. Typically, such tests of ductless units are a contrivance used for the limited purpose of verifying contaminants are not leaving through the operating opening.
Beginning this calendar year, ASHRAE 110-2016 is undergoing periodic revision, which will probably include the formal addition of new tracer gases and a possible elimination of SF6 due to environmental considerations. Test scope is also a likely topic of discussion since it has never expanded past its limited, initial 1985 fume hood only scope.
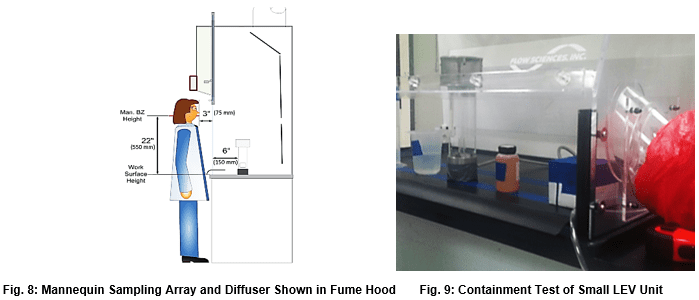
European Standard EN 14175 Part 3, 2019
EN 14175 covers construction, installation, and containment of lab hoods. It has, therefore, a much broader scope than ASHRAE 110. Here, the writer will only review Part 3 which covers testing.
Updated in 2019, Part 3 focuses on hood performance and its measurement. Most of the complex containment equipment remains unchanged from the 2003 edition of Part 3. Based on the size and complexity of the apparatus, this test does not easily travel to an operating lab or job site.
Primary concerns with EN 14175-3 include an inability to differentiate performance in a meaningful way between tested units and significant issues applying the tests under field conditions.
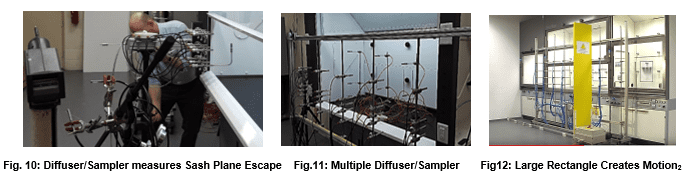
Human as Mannequin Test (HAM test)3:
This test uses ASHRAE 110 – specified equipment in a kinetic challenge to the containment cavity. Prescribed manipulation of lab equipment within inches of the operating gas diffuser are undertaken. Containment of tracer gas in the operator’s breathing zone is measured. This test rarely shows containment issues with larger fume hoods, but Flow Sciences also uses this test inside much smaller containment units with similar success. The writer views this test as an aggressive containment evaluation tool because of the programmed movement of objects around the actual tracer gas diffuser. In the writer’s opinion, the test has added an additional kinetic challenge to the tests included in ASHRAE 110.
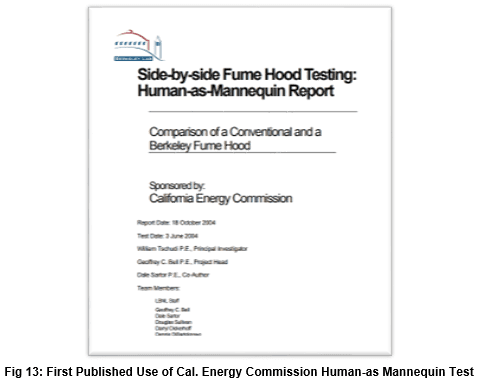
Surrogate Powder Tests:
While the previous three tests evaluate containment of vapor, powder containment has now become a huge issue for pharmaceutical and agribusiness enterprises. Because powders have unique electrostatic properties and routinely undergo grinding, sieving, and filtration operations, additional test procedures are necessary to evaluate containment devices destined for powder application. Such testing procedures will vary widely based on the characteristics of the processes being contained.
The International Society for Pharmaceutical Engineering describes the general surrogate powder approach in Good Practice Guide: Assessing Particulate Containment Performance of Pharmaceutical Equipment, Second Edition4.
In this testing approach, researchers manipulate lactose, or other surrogates, in a fashion similar to an anticipated pharmaceutical active powder as a way of forecasting the expected particulate containment. These operations may include such procedures as weighing, grinding, dissolution, and filtering.
Air pumps and filters collect room and containment area samples during the test procedure. Such pumps are located in the test lab, in the containment device, and on the experimental subjects themselves as in figures 15 and 16 below.
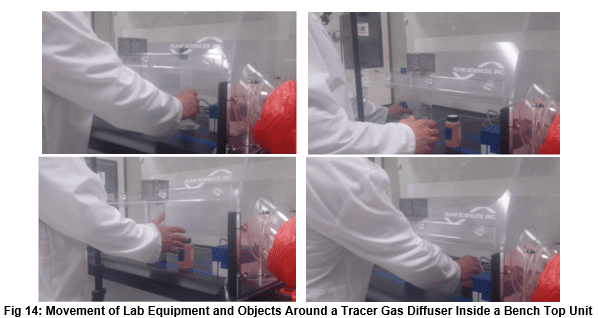
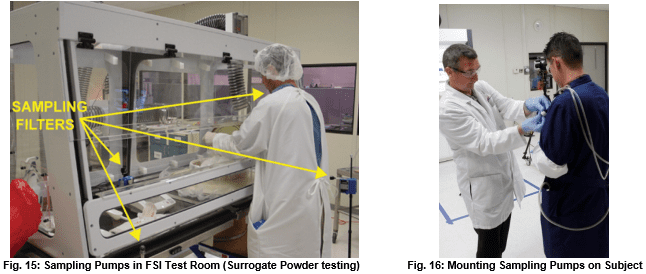
Experimenters then analyze “Loaded” filters using a contract analytical laboratory accredited by the American Industrial Hygiene Association (AIHA).
Flow Sciences reports resulting data from such tests using mg/m3 or ng/m3 in the containment cavity, the lab, and near the worker breathing zone. Research or production staff can then look to these data as indicators of work area concentration, room air contamination, and worker breathing zone contamination. Such testing therefore addresses whether containment equipment is demonstrably safe within pre-determined safety levels.
NSF 49 6:
The National Sanitation Foundation (NSF) completed the NSF 49 standard for testing Class II biosafety cabinets in 1976. This standard evaluates a cabinet’s ability to contain biological contamination while also preventing the outside environment from contaminating samples within the cabinet. Class II biosafety cabinetry should be capable of minimizing the hazards inherent in working with biosafety agents of levels 1, 2, 3, or 4.
NSF/ANSI 49 includes basic requirements for design, construction and performance to provide personnel, product and environmental protection; reliable operation; durability; cleanability; noise level and illumination control; vibration control; and electrical safety.
In addition, the standard includes detailed test procedures involving nebulized and sprayed Bacillus Subtilis Niger as a representative surrogate bacteria and open agar petri dishes as the detection mechanism. NSF has an internet informational site, including recommendations for installation, field certification tests and decontamination procedures. The NSF website contains a biosafety cabinet index for all approved units, describing all flow metrics that will produce the proper flow to shadow parameters used to certify the original cabinet design 7.
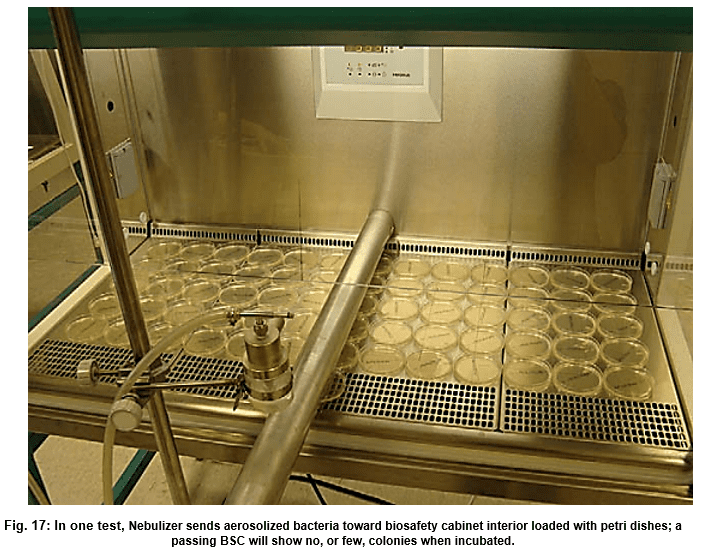
Conclusions and Predictions:
The writer again shows Table 1 below; it lists the five tests used to evaluate the containment devices we have discussed in this white paper.
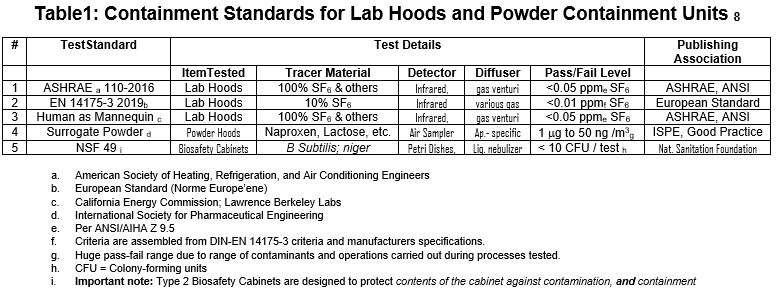
All these tests provide necessary data to research and pharma/manufacturing clients wishing to assess containment safety. The following section reviews these tests and points out where each one is most useful:
American labs and drug manufacturing facilities all use ASNS/ASHRAE 110-2016 to evaluate chemical fume hoods. Other smaller filtered and unfiltered containment devices frequently face these tests as part of a less formal but equally relevant battery of evaluations.
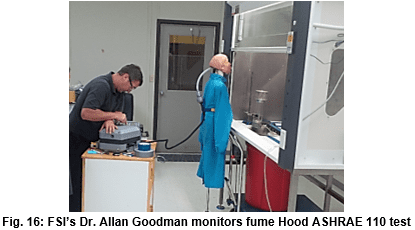
In Europe and other regions on our planet. EN 14175 definitively evaluates lab fume hoods, sharing the same scope with ASHRAE 110: fume hoods. However, the specific equipment prescribed in these tests makes it difficult to use this standard to evaluate smaller non-fume hood devices, while the complexity of the equipment makes field evaluations time-consuming and proceduraly difficult.
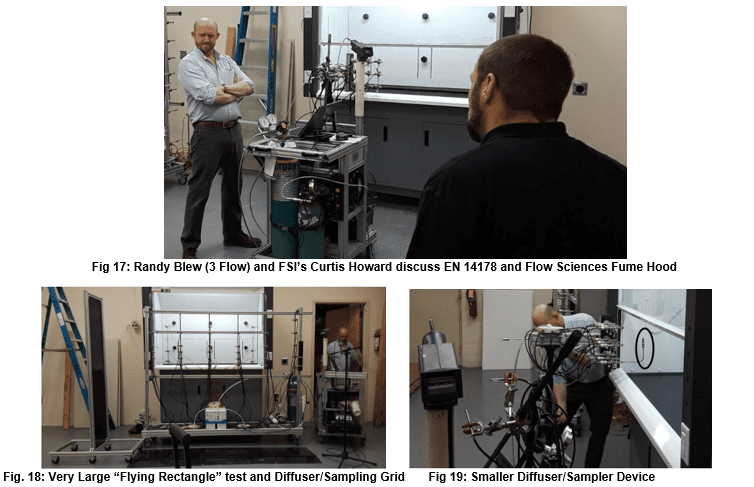
The Human-as-Mannequin (HAM) test is the most frequently used supplementary test when using ASHRAE 110. HAM specifies the same equipment and tracer gas as ASHRAE 110. While kinetic movement inside the work area described in HAM is relevant to containment performance, such a test is not present in ASHRAE 110. Therefore, this test adds a significant kinetic challenge to the ASHRAE 110 methodology.
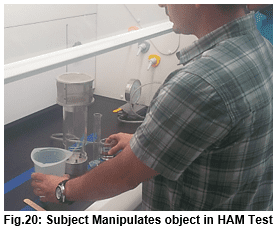
Surrogate powder tests evaluate powder containment and should always be included in any test protocol where finely divided powders are present. Flow Sciences and our clients have insisted on this for years. Powders do not propagate in the same way as tracer gas. Electrostatics can promote containment issues if powders stick to hands and arms inside the containment area and then are withdrawn.
Manufacturing sites using highly potent pharma ingredients must have high confidence in the containment of large quantities of such products during manufacture. For this reason, Flow Sciences frequently runs surrogate powder tests at our facility with functioning equipment and personnel simulating production operations with surrogate powders.
For powder use, surrogate powder testing will continue to be the primary criterion for evaluating containment equipment manufactured by Flow Sciences.
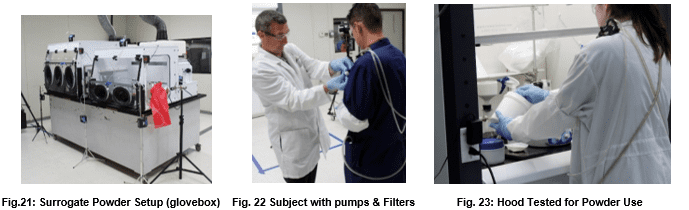
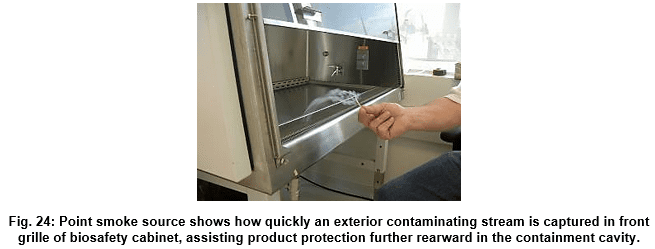
We can break down all these tests two ways to better understand the scope they cover in containment testing:
Simple and portable vs. complex and awkward: ASHRAE 110 and HAM tests are simple and portable; EN14178, surrogate powders, and NSF 49 are much more complex and not amenable to field use. Using tracer gas (molecular) techniques has led to simple equipment (ASHRAE 110 diffuser), which leads to lots of comparable data. Complex equipment using gas diffuser arrays and moving rectangles on tracks are inherently less capable of generating comparable data from one device to another. Complex equipment also is very difficult to use in the field.
Molecular tracers vs. living tracers: ASHRAE 110, EN14175, and the Surrogate Powder tests all use molecular tracers; NSF 49 uses living tracers.
Overall, the author has set forth containment testing protocols used to evaluate a wide variety of containment devices. There are several impacts this study has upon what direction such testing might take in the future.
The following diagram plots all these tests into a distribution continuum.
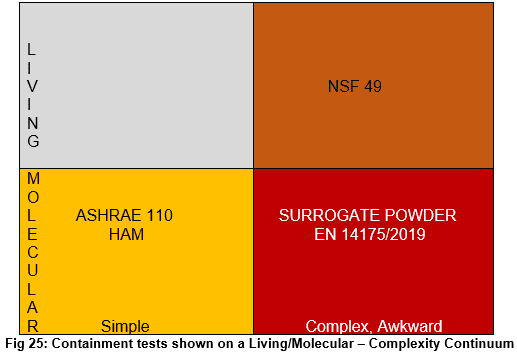
Simple molecular tracer tests are so widely used that much performance data is available. We read, compare, and study such data and deduce trends from one containment device to another with some validity. Such deductions are the first step in formulating reliable pass/fail standards for such equipment. All of this is good.
Currently devices evaluated with surrogate living organisms (bacteria, virus, etc.) or molecular powders present a more problematic array. We may use different powders or organisms as tracing agents. We can undertake different kinetic challenges based on procedures and customer requirements. We may have greater or lesser containment goals based on the virility or toxicity of the material we aim to isolate. These inherent differences in procedures and containment goals mean each test becomes unique. While each containment test may have successful results, generalizations will always be difficult from such a success to yet untried applications. All of this robustness in procedures and tests leads to fewer universal truths. Tests with powders or biological tracers do not readily spawn generalizations.
This challenge does not reduce the usefulness of biological or surrogate testing, but it does increase the work necessary to validate each new product! Be sure to research your chosen containment unit thoroughly; have the people who built and installed it relevantly and thoroughly tested its performance?
Footnotes:
- The Galaxy of All Containment Devices, Flow Sciences White Paper, 2019, Flow Sciences Inc., Leland NC., p. 16
- Waldner Video, EN14175 Kinetic Test, https://www.youtube.com/watch?v=VpkDBAsgQpc
- Side-by-Side Fume Hood Tests Using ASHRAE-110 and Human-as-Mannequin Test Methodology, 2005, Exposure Control Technologies, Inc, Carey, NC.
- Good Practice Guide: Assessing Particulate Containment Performance of Pharmaceutical Equipment, 2nd Edition, 2012, International Society for Pharmaceutical Engineering.
- Two Well-Known Fume Hood Tests, Robert Haugen, 2018, Flow Sciences, Inc.,p.2, https://flowsciences.com/two-well-known-fume-hood-containment-tests-ashrae-110-en14175-a-comparison/
- https://www.nsf.org/services/by-industry/pharma-biotech/biosafety-cabinetry/nsf-ansi-49-biosafety-cabinetry-certification
- http://info.nsf.org/Certified/Biosafety/Listings.asp?
- Because of diverse standards and countless pass-fail criteria, glove boxes and isolators are not included in this review of containment standards.
- International Standard, ISO 14644-7, “Cleanrooms and Associated Controlled Environments” Part 7 Separative Devices (Clean Air Hoods, Gloveboxes, Isolators and Mini Environments) (2004). International Standard, ISO 14644-7, “Cleanrooms and Associated Controlled Environments” Part 7