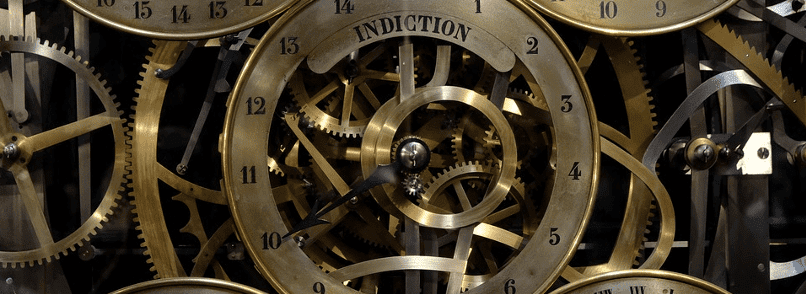
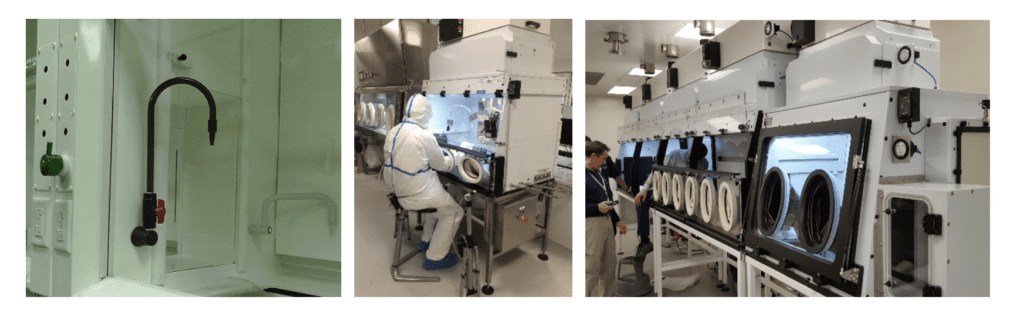
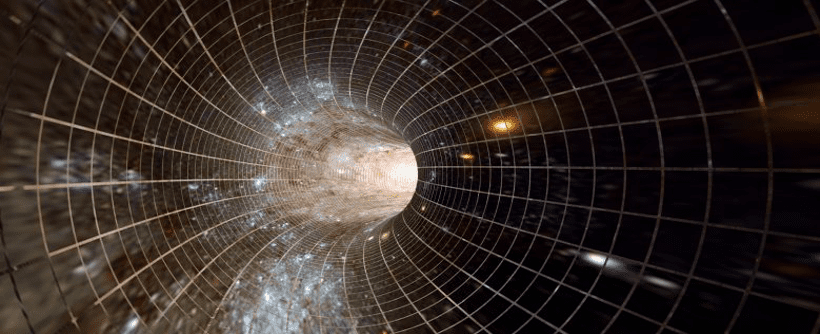
Dr. Robert Haugen
Flow Sciences, Inc.
6/11/20
Abstract:
Today, we all find ourselves in a reflective mood! Our business is, after all, containment. Covid 19 and we are therefore at cross-purposes! Many other more general trends in pharmacy and bioscience also cause us now to reflect on our future.
Where is the lab containment going in the next ten years? What contemporary extract products have a future? How will this health crisis help us refine our methods and objectives? What meager portion of our inventive genius will remain after we encounter the value engineering committee?
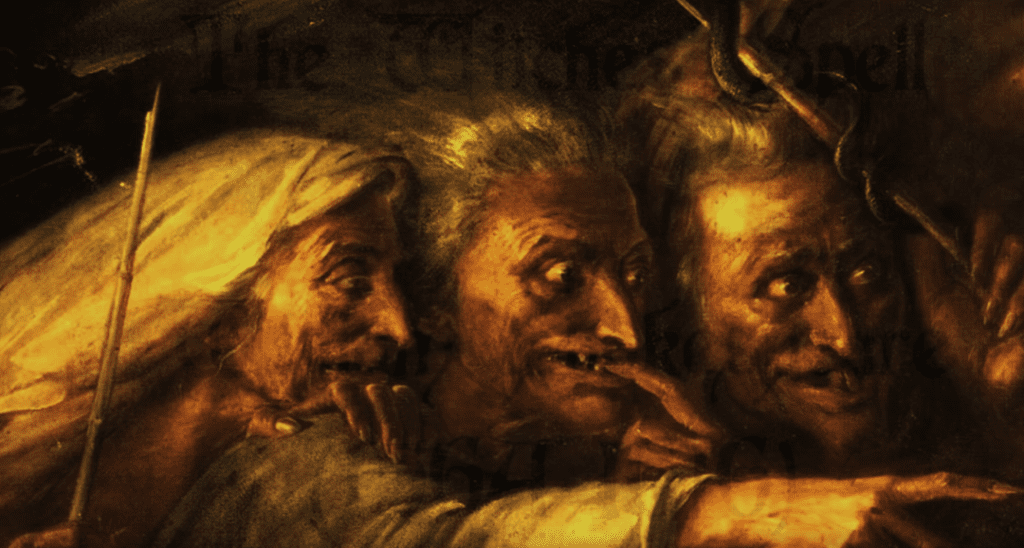
Fig 1: Typical VE Session at Cawdor Castle
These are the questions explored in this paper. Researchers, lab safety experts, pharma production designers, architects, planners, and of course, purchasing agents all have their own takes on such topics and their own unique influences on what will eventually happen.
While the writer aims to take an impartial approach to this topic, he is aware that forecasts tend to be largely autobiographical!
The Present: Successes and Challenges:
From 2000 to 2019, many important changes have changed the laboratory design industry.
- Successes:
In the past decade, containment improvements in lab equipment at lower exhaust volumes has been a chief focus. For example, acceptable control levels on fume hood ASHRAE 110 tests in the field are now recommended by ANSI Z 9.5 as 0.050 ppm “as installed”1 and in some job specifications even lower 2. This level is dramatically lower than the basis of testing at the end of the 20th Century, which was 0.10 PPM 7.
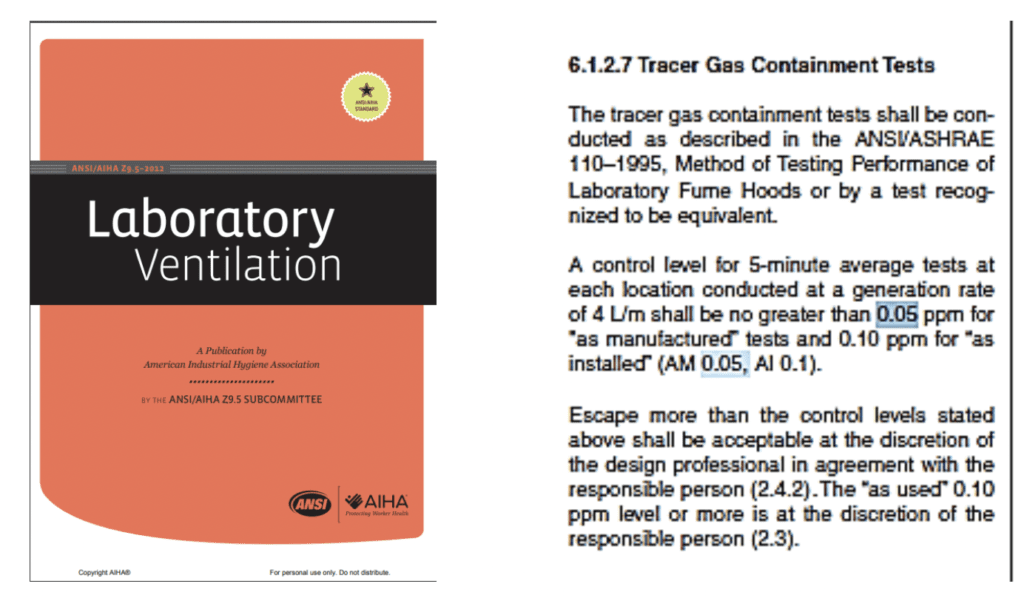
These more rigorous control levels now apply to fume hoods exhausting much less air. While 100 FPM was the ‘acceptably safe’ flow in past decades, we now expect modern fume hoods to function effectively at anywhere from 60 FPM to 80 FPM. 6
The industry now evaluates portable and smaller exhaust hoods using ASHRAE 110 methodology, even though the test document does not include many of them by definition. We also frequently measure containment of filtered powder hoods with exhaust thimble connections, and many purpose-built pharmaceutical production containment units even though ASHRAE 110 does not include these either.
All such FSI units test out on ASHRAE 110 at < AM 0.05 ppm. Many of these units have also been field tested (AI). In short, product-demonstrated containment as expressed by ASHRAE 110 has historically gotten tighter, while units tested by ASHEAE 110 are many times not within the scope of the current standard.
Figure 2: Local Exhaust Hood (LEV III)
Figure 3: Balance Enclosure, Fan & Filter
Figure 4: Chemical Fume Hood
Other containment tests that directly measure particles, not tracer gas, have also gained general recognition in the pharmaceutical field. Such rigorous performance standards are individualized and context-specific. Our customers routinely apply these standards in the field under operating conditions with face velocities in the 60 FPM to 80 FPM range.
ISPE 3 methodologies are good examples. These techniques use kinetic operational testing with a selected surrogate powder using filtered air samplers in the application area, on the research subject, and inside the lab hood. These samplers collect particles that have remained inside containment, or escaped containment over the length of the procedure. “Procedures” usually simulate activities done in the relevant pharma production or research setting. Grinding, sampling, weighing, and powder transfers are all activities typically incorporated into a surrogate procedure. The measured short-term exposure limit (STEL) must stay under a certain pass-fail level, generally in the fractional mg/m3 range. Flow Sciences has actually used pass/fail levels as low as 1.0 ng/m3! The possibility of achieving control levels in this range is good news for working area laboratory air quality and system sustainability! The challenge with these hyper-specific methodologies is that they are difficult to generalize from precisely because of their specificity.
Fig. 5: FSI Surrogate Powder Fume Hood Test
Fig. 6: FSI Surrogate Powder Test on Bag-In Bag-Out Multiple Containment Devices
- Challenges of the present:
Insistent rumblings for changes in containment requirements are already in the air! Pharmaceutical production of highly active drugs is increasing 4. Examples are genetically specific drugs with high potency, which require smaller containment devices with rigorously low short-term exposure limits. As such challenges face our industry, an increased demand for monitoring low levels of allowable background contamination, documenting maintenance, memorializing SOP’s, and requiring customer support by the manufacturer are all critically prominent!
The Future; Directions for the Next Decade:
As the writer sees it, the next decade is pointing in several exciting and challenging directions for evaluating containment. The author has listed these in their perceived order of importance:
- New containment requirements in pharmaceutical production will mandate much lower short-term exposure limits (STEL’s).
As mentioned previously, very low STEL’s are on the horizon for highly active pharmaceutical ingredients (HAPI). These low requirements, possibly in the ng/m3 range, will probably change the types of containment devices used to house manufacturing equipment involved in making these products. The containment devices will therefore most likely transition from access openings to gloved enclosures
Figure 7: Buchi B-290 Mini=Spray Dryer for API Processing
Figure 8: Glovebox and Fitzmill for HPAPI’s
- The Covid 19 Pandemic will require rapid crisis development and dissemination of vaccines and medications aimed at disease treatment and elimination.
While the United States Pharmacopeia has written a “new” standard, USP 800, USP typically does not enforce this standard. Uncertainty about levels of enforcement has resulted in legal challenge to the standard. While USP 800 is technically active, it is essentially advisory, until the legal challenges are resolved.
This scenario may truncate many pharma SOPs in order to make Covid 19 medicine quickly. This resulting rush could degrade containment and product purity standards.
The author anticipates that the Occupational Safety and Health Administration, some state pharmacy boards, and some state laws will eventually mandate a yet-to-be-determined standard once production pressures subside. It is the author’s belief that USP 800, or a derivative, will probably become a regulatory standard within this decade. This will be welcome news for those workers charged with safely producing or testing pharmaceutically active ingredients on a daily basis.
The author anticipates such a resulting successor to the currently unrecognized USP 800 will require personal protective equipment in many contexts for administration of hazardous drugs to contagious patients. It may also mandate the use of protective medical equipment like closed-system transfer devices, needleless equipment, and plastic pouches for pill crushing. 5
For hospitals, pharmacies (particularly compounding pharmacies), and other institutions that compound, administer, or manufacture pharmaceuticals, this new standard may require many facilities to upgrade procedures and acquire additional containment equipment to support and improve current activities. Increased personal protection will also become mandatory for staff who mix various pharma products together to meet specialized prescriptions.
Sterile product evaluation will undoubtedly also become involved in these changes.
- Lower exhaust rates for most containment will probably hit practical lower limits this decade.
Exhaust levels in laboratories will continue to decrease. Containment requirements in labs and production facilities will continue to increase. At some point, these two trends will create a collision or achieve some sort of negotiated equilibrium. We will probably wind up balancing sustainable extract levels against minimal building needs such as sensible heat loads or tolerable room air quality.
Conclusion:
Today, Covid 19 is a huge shaping factor for science, pharma, medicine, social planning, architecture, religion, education, politics, media coverage, and transportation.
What have I forgotten? Entertainment, sports, retail purchasing, auto sales, travel, history, archeology, and paleontology.
Everything. Absolutely everything. In no particular order.
In such an environment, hope must focus on tools, time, and ideas:
Tools that are generally useful, time to support research, and ideas that require development and expression through experienced engineering. We are prepared to face this future with containment equipment ready to ship now (tools). Such equipment will help meet urgent needs and buy us time. Our highly skilled, degreed and published design engineers address new perceived needs and move forward with adaptive ideas and appropriate means to build products and test them.
TOOLS
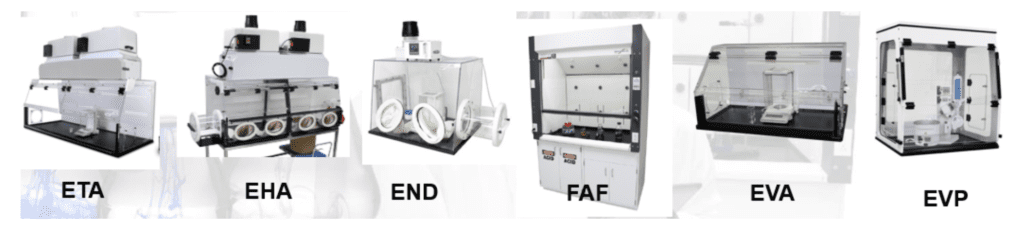
TIME
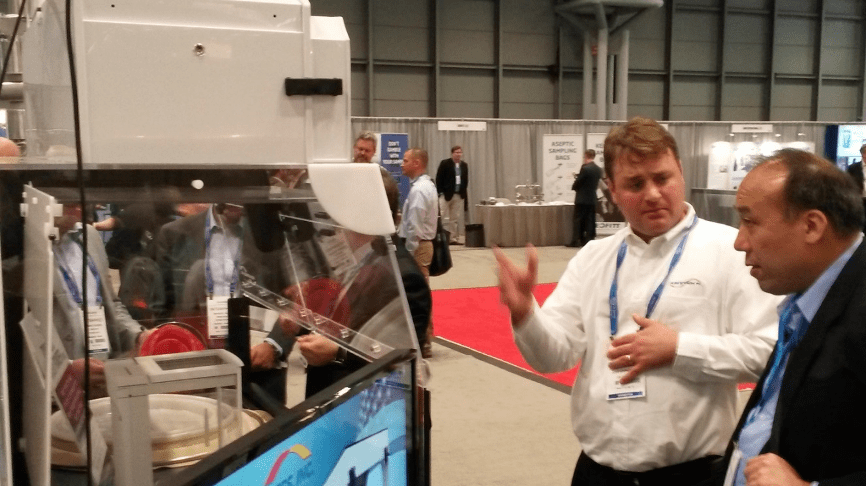
NEW IDEAS
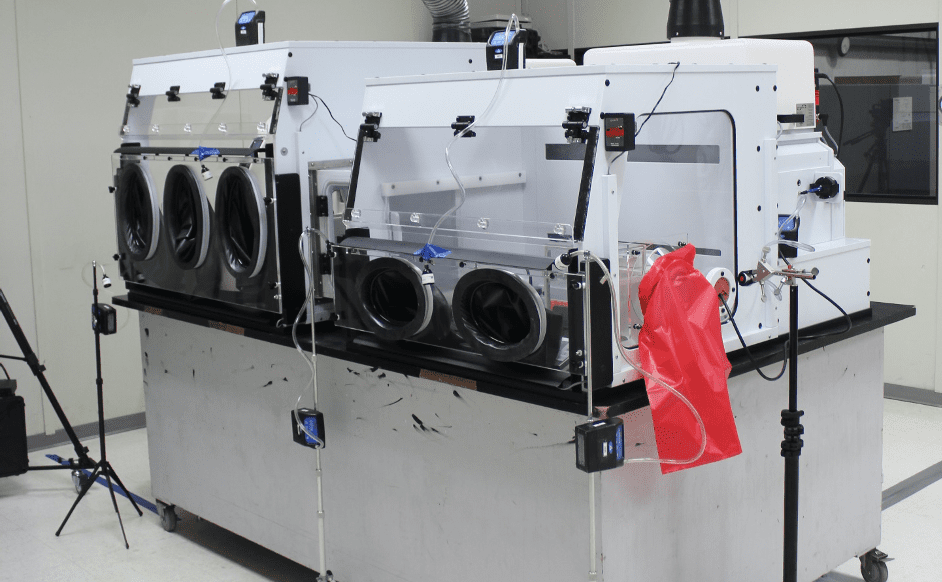
After the chaos subsides, and it will, we will need to be forward-looking but cognizant of new challenges that may lurk in our future. Challenges capable of Covid 19 repercussions. Challenges waiting to reset all our expectations about our futures and convenient laws exposed as being irrelevant. Something waiting to provide opportunity for all of us to progress the human condition if we embrace it!
Footnotes:
- ANSI/AIHA Z 9.5, Tracer Gas Containment Tests, 2012, P. 72, Section 6.1.2.7
- In most cases because of limitations of SF6detection, lower containment numbers are attained by running the gas flow rate into the fume hood at 8 lpm rather than 4 lpm.. Other steps are used to complicate the hood interior by adding cans and other obstructions (Merck Rahway spec section 115315)
- Assessing the Particulate Containment Performance of Pharmaceutical Equipment, International Society for Pharmaceutical Engineering, 2012, Chapters 1-8
- FDA Perspective on Continuous Manufacturing, Sharmista Chatterjee, IFPAC Annual Meeting,Baltimore, 2012, p.2 https://www.fda.gov/files/about%20fda/published/FDA-Perspective-on-Continuous-Manufacturing–Sharmista-Chatterjee–Ph.D.–January-22–2012–IFPAC-Annual-Meeting.pdf
- Best practices for the safe handling of hazardous drugs — How to prepare for USP 800, McKesson Health Care Company,
- ANSI/AIHA Z 9.5, Tracer Gas Containment Tests, 2012, P. 23, Section 3.3.1
- Using the ASHRAE 110 Test as a Tool to Improve Laboratory Fume Hood Performance, Hitchings and Maupins, 1997, p.23, https://www.semanticscholar.org/paper/Using-the-ASHRAE-110-test-as-a-TQM-tool-to-improve-Hitchings-Maupins/4e828cb00c3cc66738f03d9a17f1321637a994d2