Robert K. Haugen, Ph.D.
Director of Product and Technology Development
Flow Sciences, Inc.
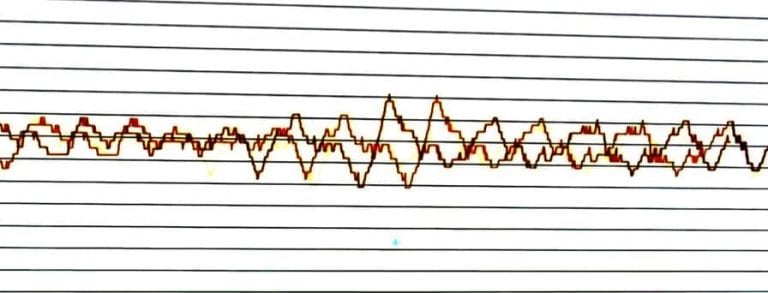
Background:
It is crucial in analytical environments that precise weighing takes place inside containment where potent powders being weighed do not escape into the lab. This is typically accomplished with a top-mount safety containment system such as the one shown below.
An effectively designed unit must have an exhaust fan and HEPA filter located at the top of the unit, and such a fan has an inherent vibration. If undamped, this vibration can significantly affect the accuracy and stability of the balance.
Any top-mount safety containment system must therefore accomplish two objectives which are at cross purposes: use air movement and a fan to accomplish protective containment while maintaining a vibration-free weighing zone to assure balance accuracy.
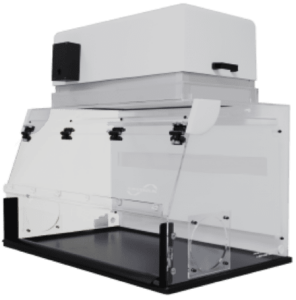
Flow Sciences incorporates a low vibration fan subassembly in its design by using a balanced fan, thicker low static pressure filters which put less strain on the motor, and a soft gasket junction between the fan subassembly and the containment unit.
The purpose of this paper is to measure the effectiveness of these three vibration isolation strategies.
Procedure:
• Determine a reasonable base line of vibration inside our product test area.
Base line measurements are made using a sensitive 3-D vibration measurement sensor attached to a Rigol DSI 052E oscilloscope. The sensor is attached to a large block of granite on the test area floor and the resulting 3-D vibration is measured and results recorded over one second. Vibration is measured in G-Force (M/sec/sec).
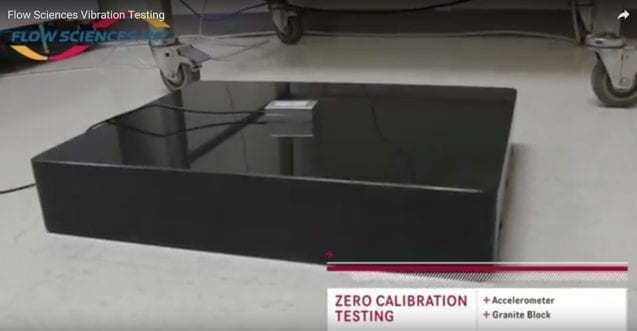
• Determine an un-dampened vibration level for the fan and its metal housing by placing the 3-D vibration measurement sensor on top of the housing while the fan is operating at a speed necessary to achieve the design face velocity in the containment unit of 70 FPM (0.35 m/s).
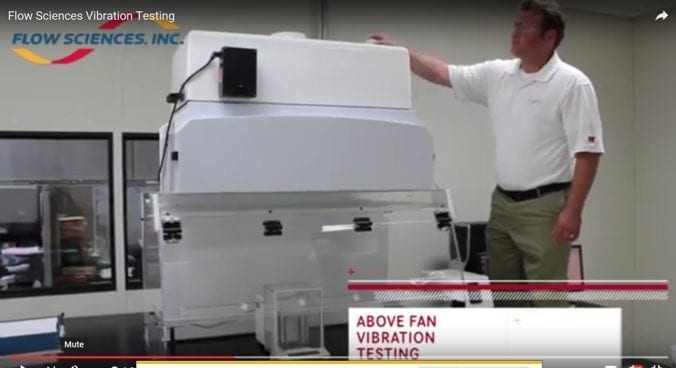
• Determine a normal damped vibration level inside the containment area by placing the sensor inside the hood on the work surface front of the containment area. The same fan operating conditions outlined in step 2 above are used during this test (70 FPM).
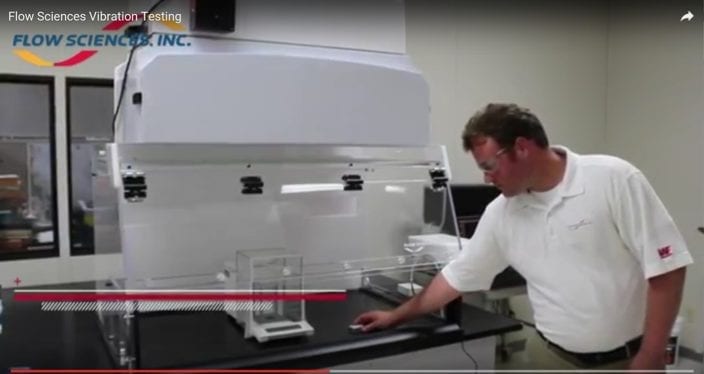
• Determine a maximized un-dampened vibration level for the fan and its metal housing by placing the
3-D vibration measurement sensor on top of the housing while the fan is operating at full speed (approx. 140 FPM).
• Determine a dampened vibration level for inside the containment area by placing the 3-D vibration measurement sensor inside the hood on the work surface near the front of the containment area while the fan is operating at full speed (approx. 140 FPM).
• Determine an un-dampened vibration level for an adjacent “noisy” piece of common apparatus by locating a Jaansun 300 Capsule Machine 1 foot away from the ETA482424AAA containment device and mounting the 3-D vibration detector on top of the unit. Fan on containment unit is left off.
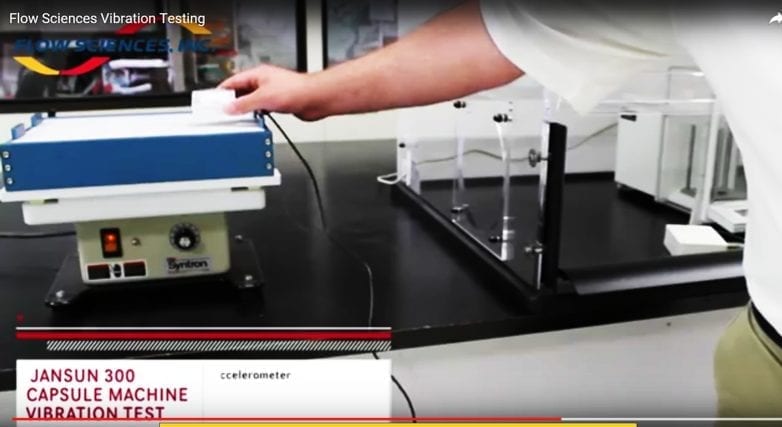
• Determine a normal damped vibration level from the Jaansun inside the containment area by placing the sensor inside the hood on the work surface near the unit front face. Fan is off. Jaansun machine remains at 50% power.
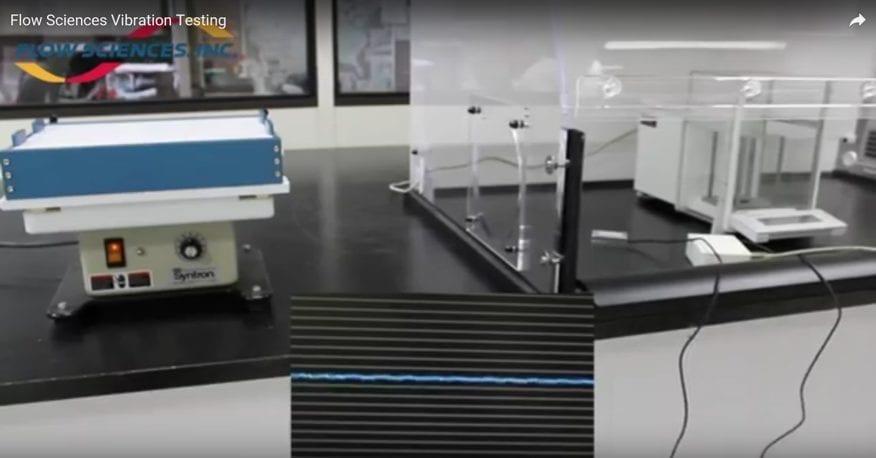
• Determine a sudden impact vibration on the fan unit of the ETA482424AAA containment device by dropping a ½” steel ball of 8.35 g mass from a 2 foot distance on to the top of the steel fan unit. Impact vibration measured by sensor placed at fan centerline. Fan is off.
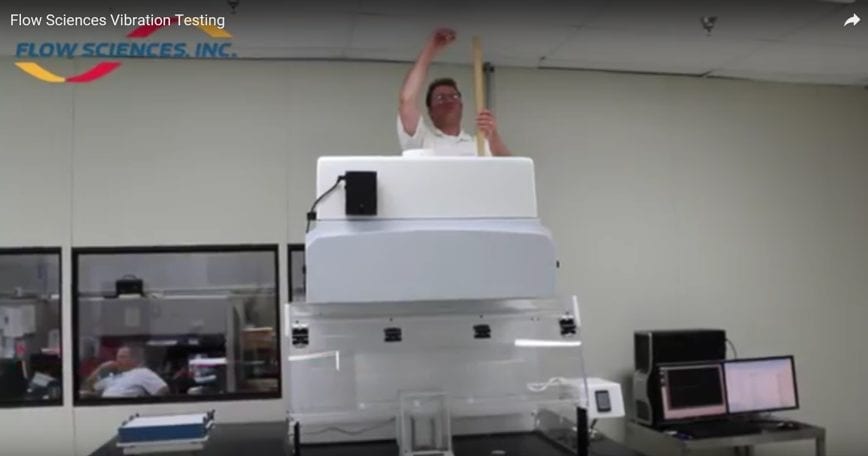
• Determine a normal damped impact vibration inside the containment area by repeating the ball drop experiment in number 8 but placing the sensor inside the hood on the work top near the front of the containment area. Fan is off.
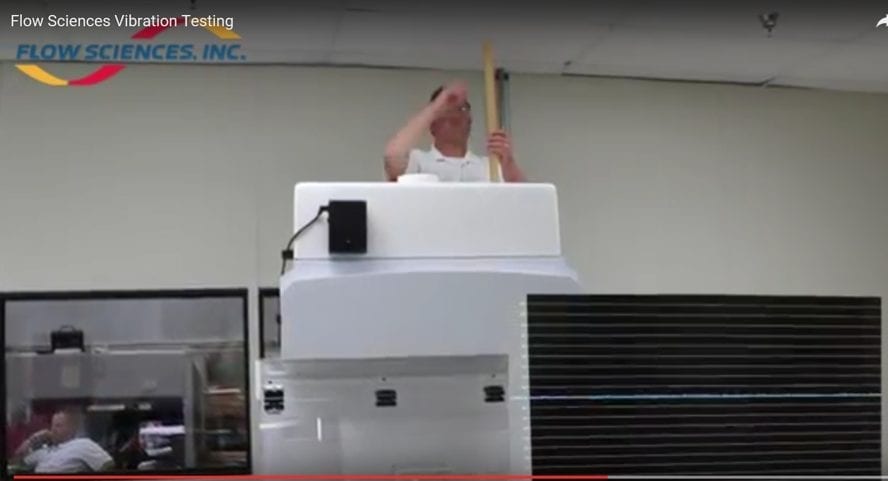
Observations:
Digital data was recorded in all three dimensions (amplitude vs. time) for all nine tests cited above. All graphs have ~ 1 second sweep horizontally.
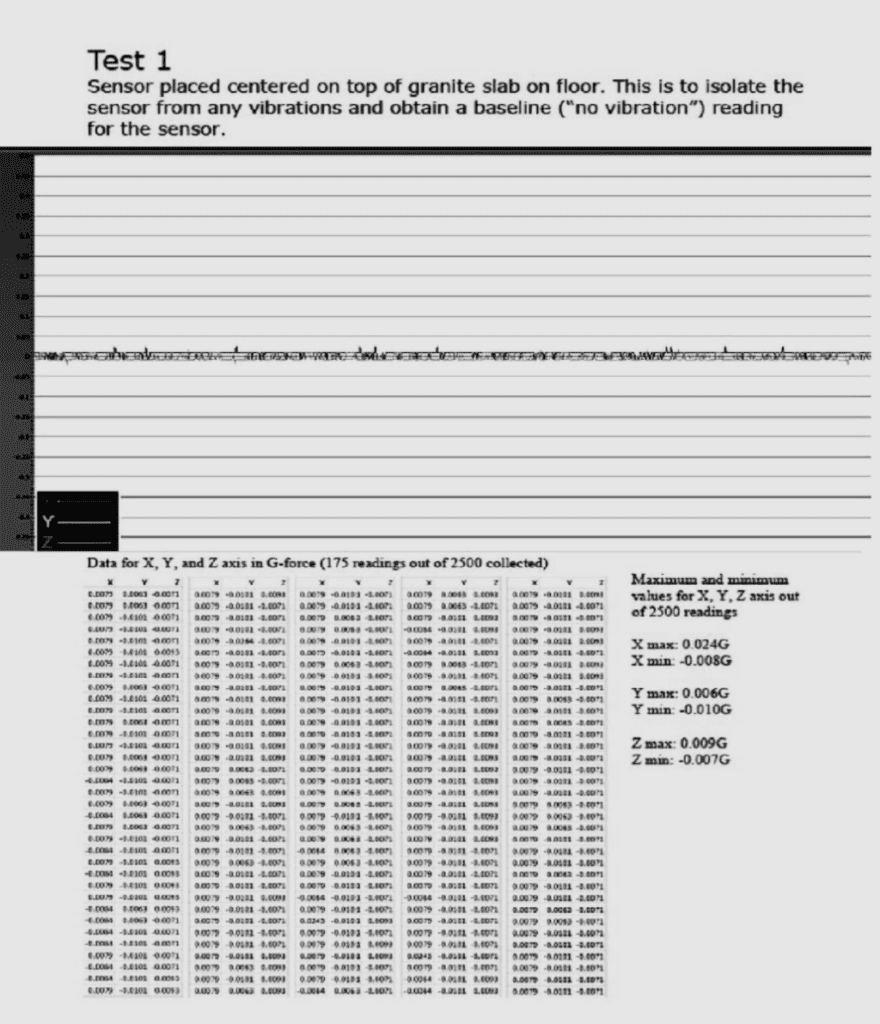
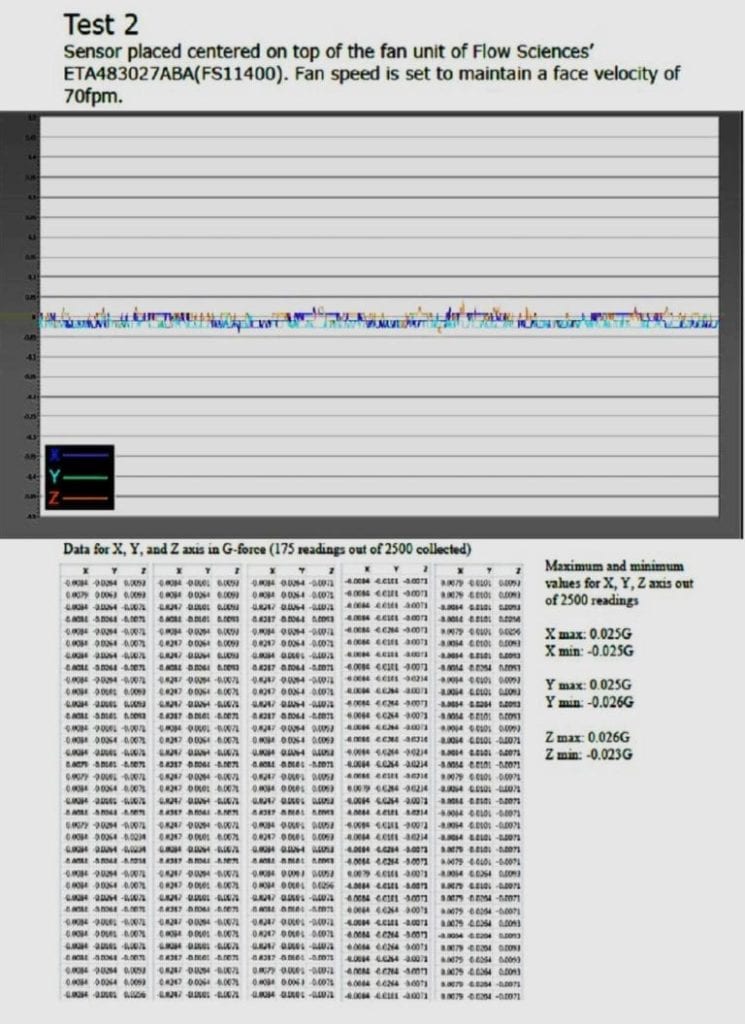
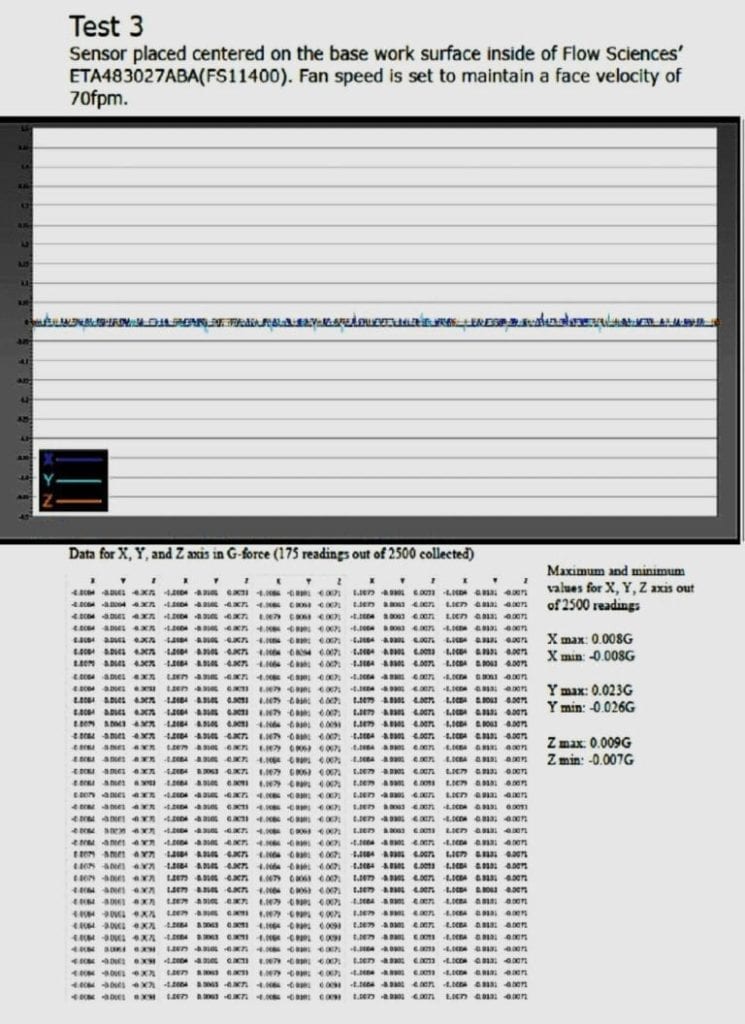
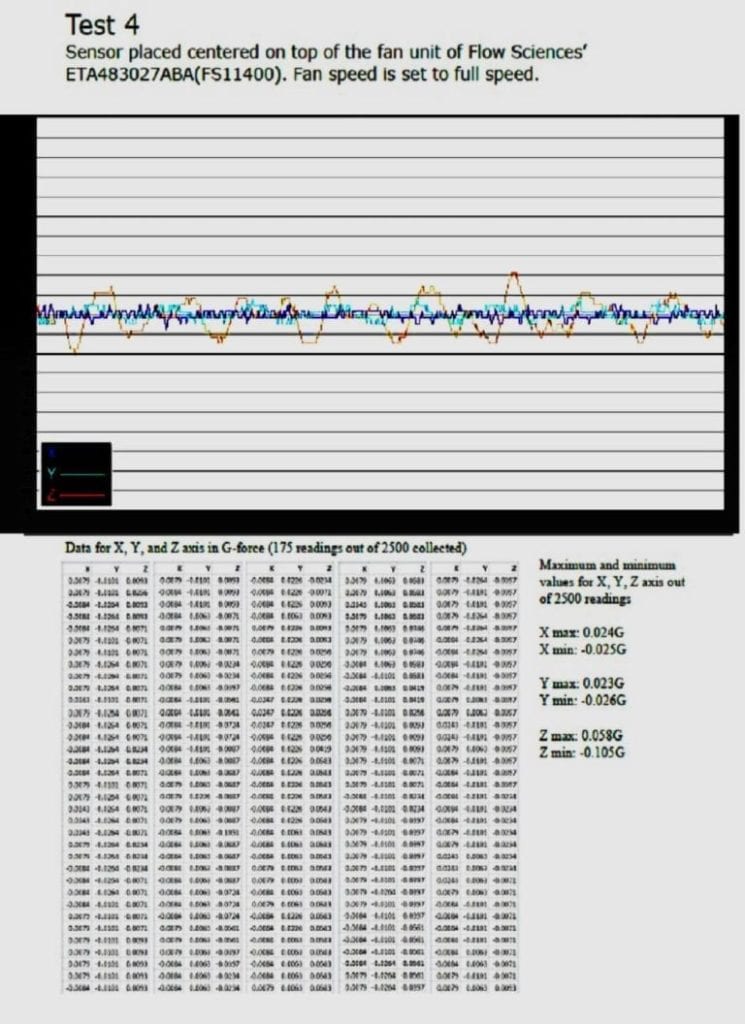
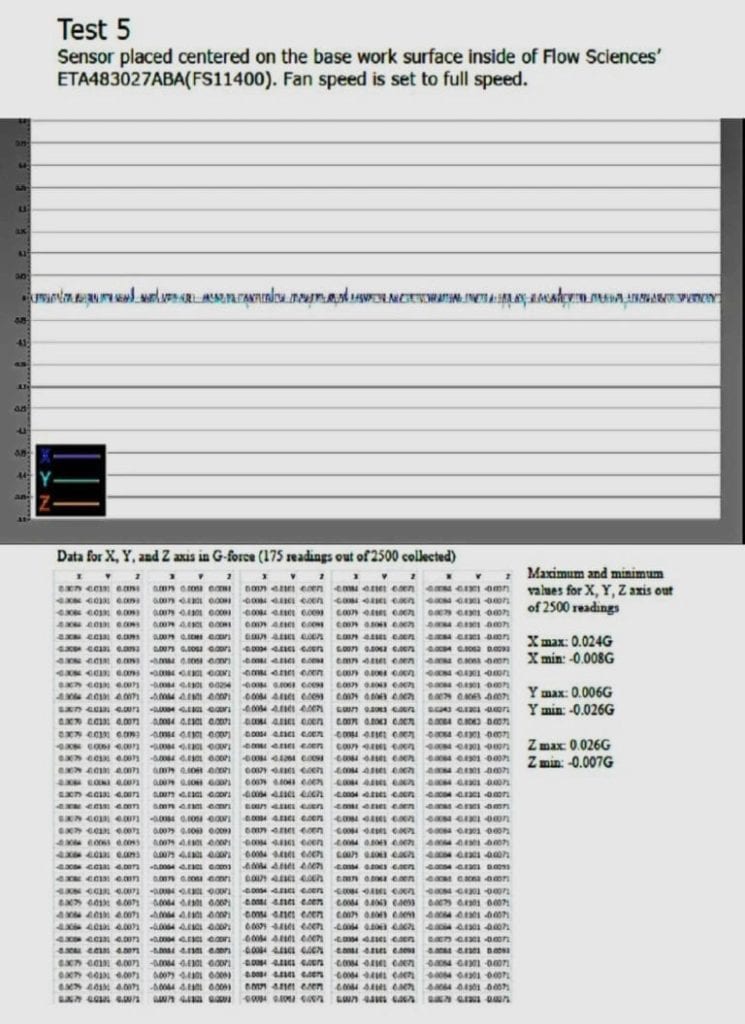
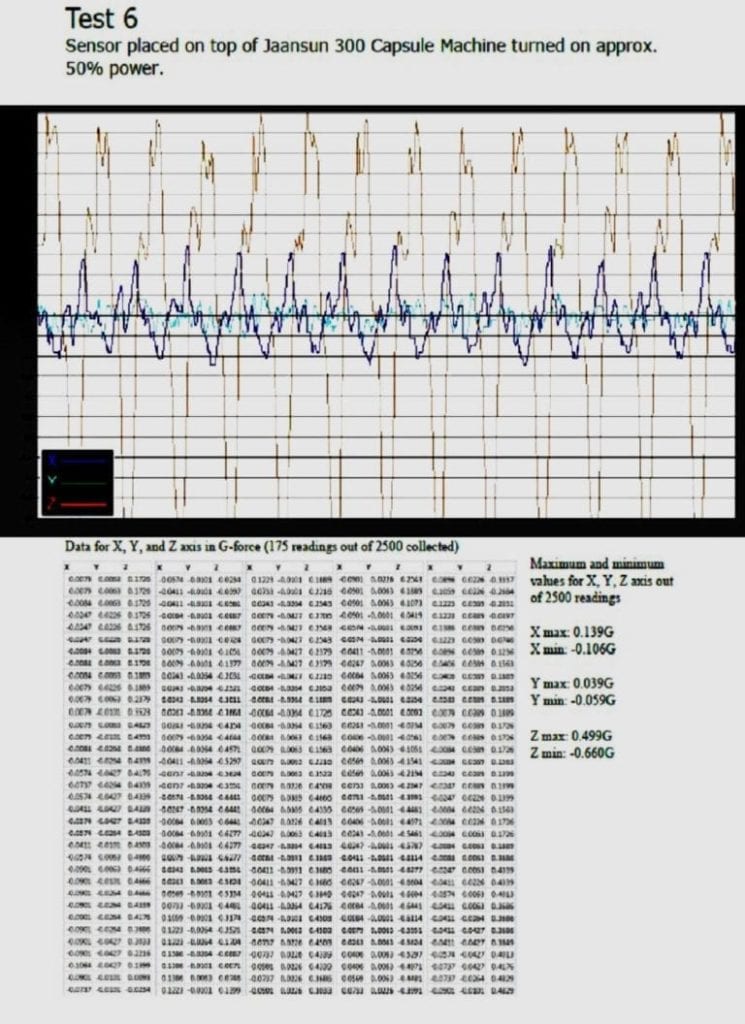
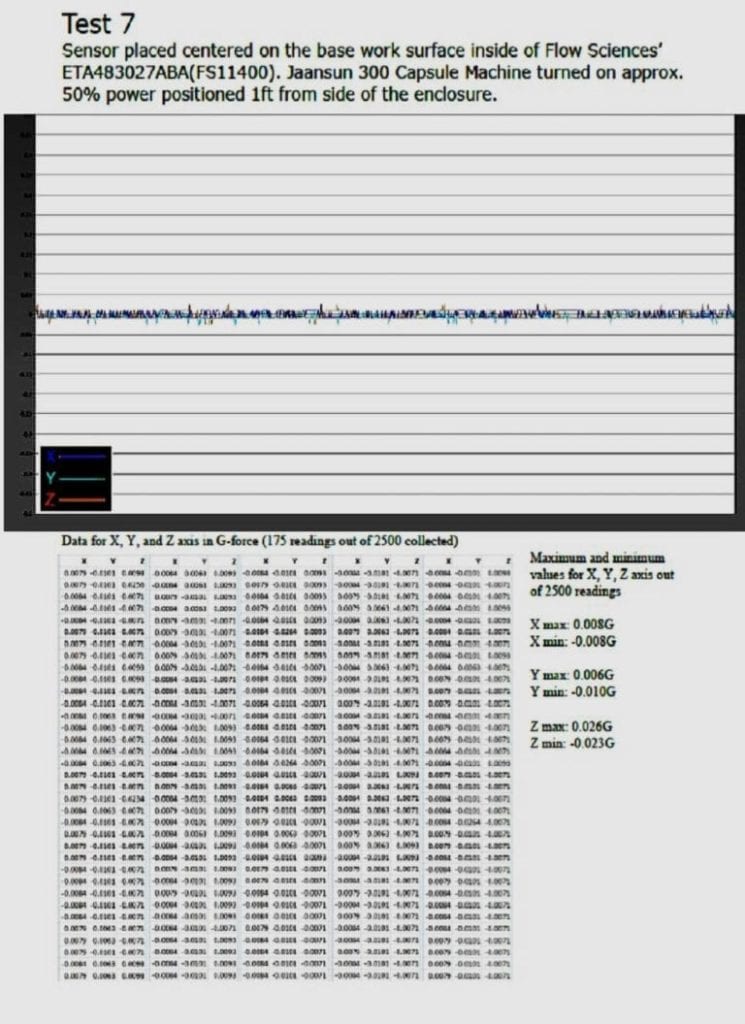
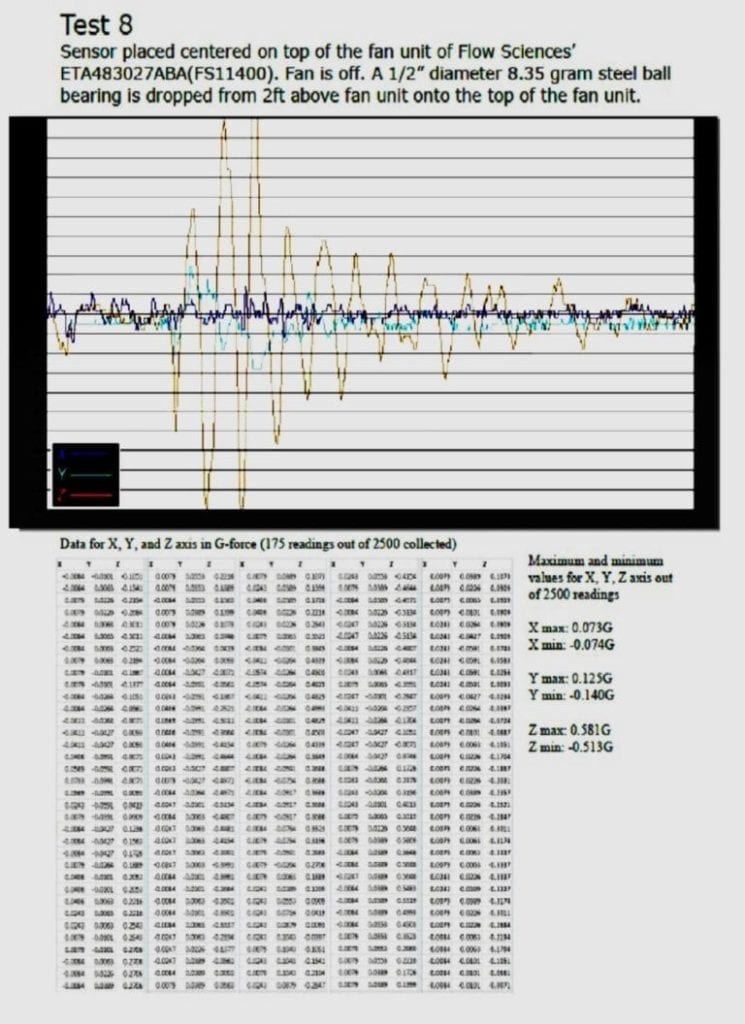
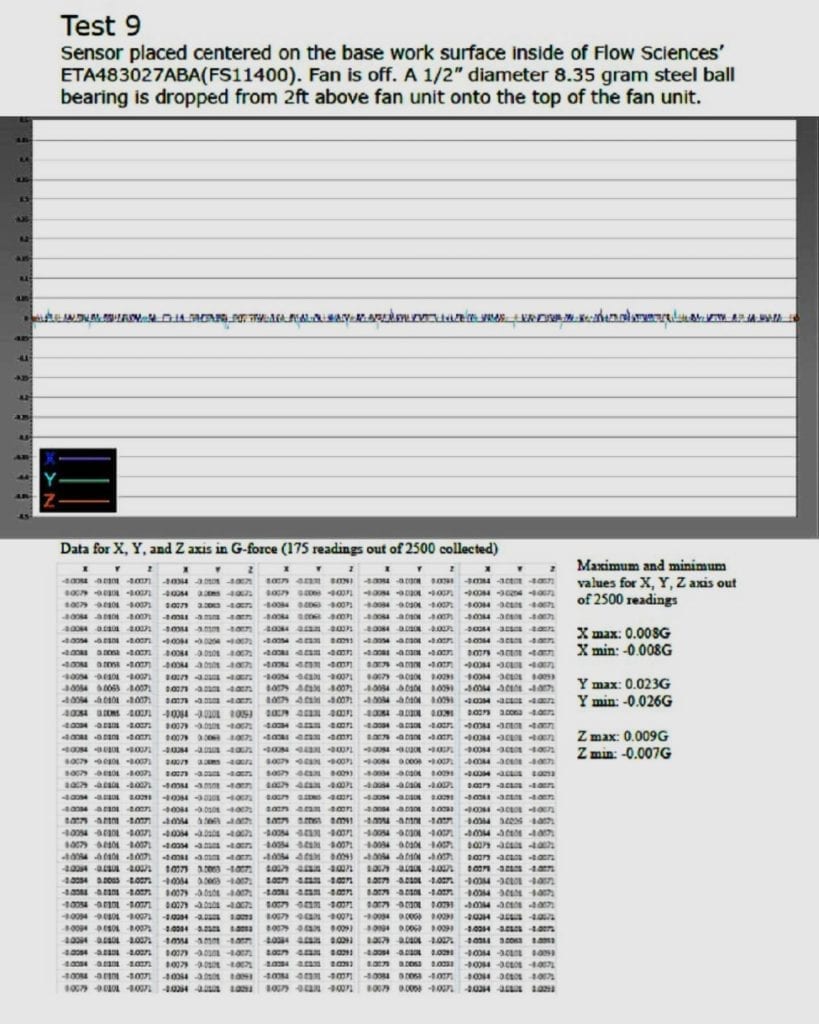
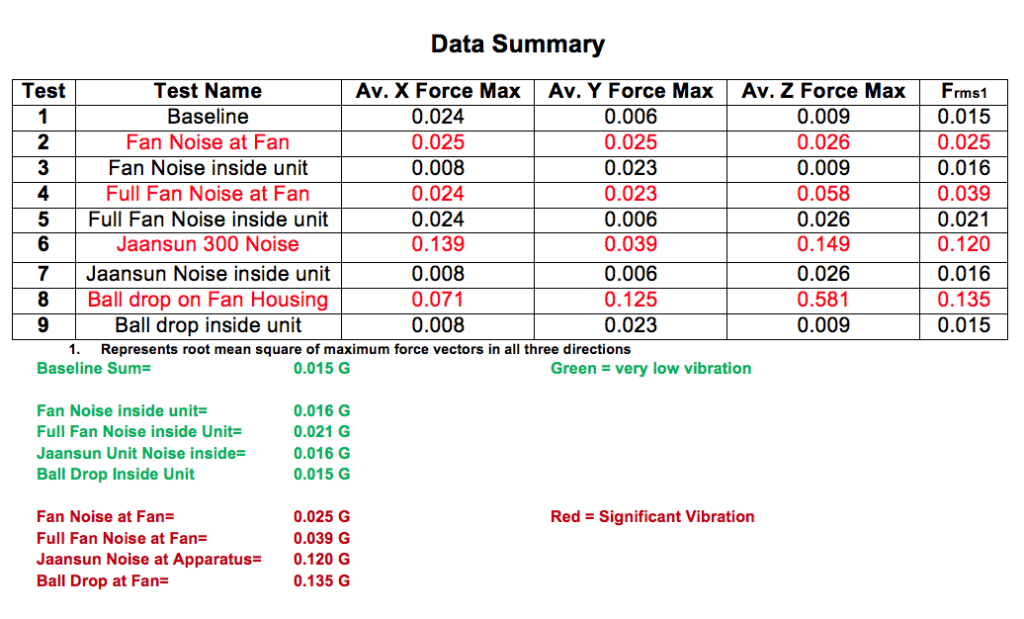
Conclusions:
1. The ETA482424AAA weighing isolation device provides effective dampening from all vibrations investigated. The “full fan rpm” was the only instance where a slight increase from the baseline vibration value was noted inside the containment area.
We believe increased static pressure drop past our filter will increase fan “work” and subsequently vibration. With units that have a lesser fan or thinner filter would see this phenomenon appear to a much greater extent than the very slight vibration increase seen in this study.
2. The vibration dampening effect of our Weighing Containment Device is achieved using a series of sound insulating materials between the steel top-mounted fan housing and the containment superstructure and work top.
3. Room and fan impact vibrations are therefore effectively dampened even when the fan is not running because the material interfaces between the vibration sources and the balance inside the containment structure still exist. Both the table-mount Jaansun Capsule Machine and the ball drop had significant vibration as measured over the 1 second sampling time as measured on the machinery, but no effect whatsoever at the balance location.
The researcher concludes that the ETA482424AAA weighing isolation device’s insulated fan unit and separate work top provide an effective material interface system for vibration damping. Other causative factors, like sound diffraction through dissimilar surfaces could also be examined in future studies.