Purpose:
Generally speaking, scientific equipment manufacturing companies that correctly perceive and then meet research customer needs will succeed. Researcher-manufacturer cooperation is vital to such success. The two entities must have a real conversation about what the researcher uses as a process and how current containment is either ineffective or not present. The designer-manufacturer then makes recommendations and proposes a solution. In many cases this proposed solution must be far more than a quotation. It must also include enough information to let the customer visualize how this product will facilitate the researcher’s application.
Problem-solvers must be involved on both sides of the interaction!
This paper cites four examples of problems Flow Sciences was able to address with a variety of standard products with unique modifications. In each case, the mutual success of our customer and Flow Sciences was achieved.
Case 1: The fume hood with a nearly invisible work area.
A research company had a basement laboratory with a custom fume hood designed to handle several volatile and corrosive organic chemicals. The equipment was older, and it was also very difficult to use because of its poorly illuminated interior and small viewing window eclipsed with glove ports.
Because this customer was overseas, a large amount of email communication was involved in answering the following questions, all of which need attention for any custom application fume hood:
1) What was purpose of the device and the processes conducted in it?
2) What are the dimensions of the current unit?
3) What chemicals are used in the device?
4) What voltages and phases of electricity are used inside this device?
5) Are explosion-proof fittings required?
6) Who is our contact person to approve final drawings?
7) Are there shipping requirements or preferences?
On similar work for any containment device manufacturer, a lengthy number of emails or phone calls is typical, particularly if you involve contractual issues such as price, delivery, and scope. What is not typical is to get into application issues as thoroughly as Flow Sciences does in its communication.
From an email exchange that exceeded 50 messages and responses, Flow Sciences determined that a modified standard fume hood could handle the customer’s application with augmented visibility, containment, and value. We were able to get approval drawings agreed to and begin manufacture shortly after our questions (and theirs) were answered. See the photos below:
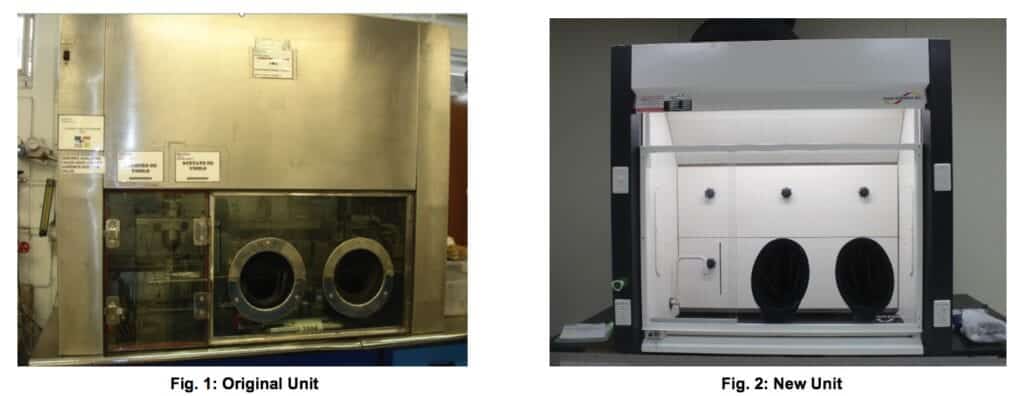
The original unit was stainless steel with two glove ports through a fixed window. The gloves in the fixed glass panel consumed most of the existing glass area allocated to viewing the workspace. A hinged outward-swinging access door on the original unit was awkward to use and increased containment issues as well.
The new unit was constructed from a combination vertical/horizontal sash Saf-T Flow fume hood with two panels. One panel housing the gloves was fixed in the sash frame, the other was a narrow sliding glass panel only 17” in width. The entire sash could be unlocked and raised vertically for cleaning and set-ups, however the hood was designed to ventilate with only the 17” wide horizontal sash available for adding samples to the hood. This sliding element caused no loss of containment when the door was opened and closed during ASHRAE 110 tests1 done at the Flow Sciences facility in Leland, North Carolina. Additionally, the custom 5’ unit was energy efficient, requiring an exhaust volume of only 233 CFM with no detectable containment loss under a variety of additional test conditions!
Case 2: The hood that suffered containment loss when heated procedures were used inside:
Many times, we are confronted with customers who find their current fume hood unable to accommodate high-temperature reactions when the sash is closed under VAV (variable air volume) operating conditions. When high temperature, VAV, and a unique procedure are all involved, Flow Sciences always asks our customer about the chemicals & procedures used and then uses the ASHRAE 110 test procedures to test containment using this process. These “seven questions” were reviewing above in case 1.
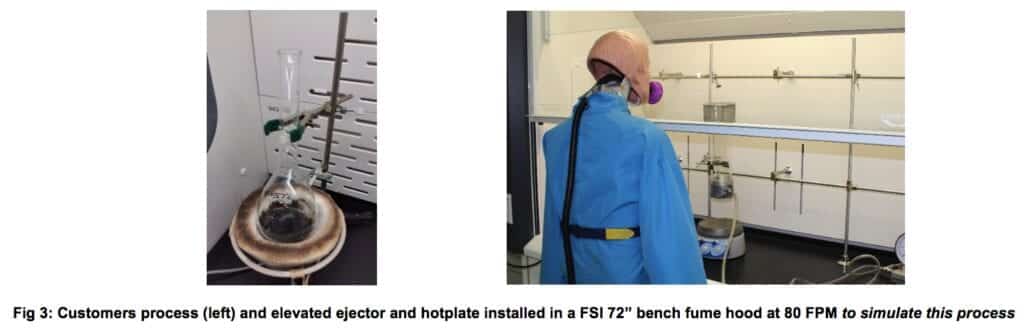
In the case depicted in Fig. 3, containment of the hood was evaluated in using the ASHRAE 110-2016 test method1 with a modified location and temperature of the diffuser. These tests were witnessed by the customer.
The hood passed all tests (figs. 4 & 5) with no detectable tracer gas leaving the containment area.
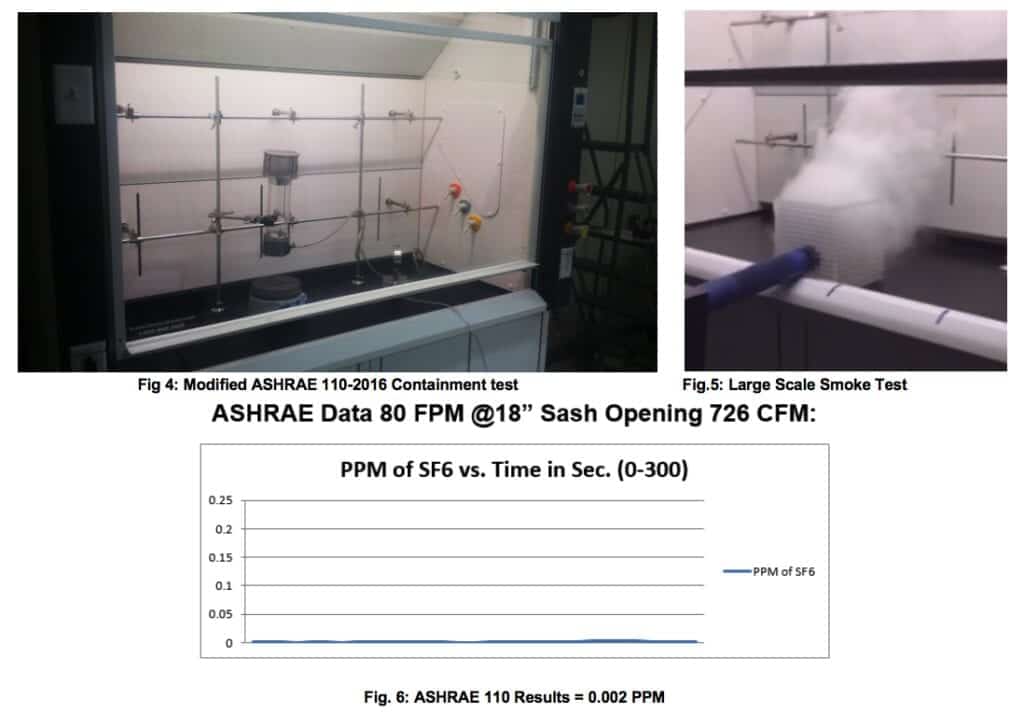
Case 3: Waste removal from animal cages.
Animal waste isolation and removal is a concern in virtually all research animal applications.
Again, we got answers to all seven questions already discussed in Case 1 from the customer. The review of these answers revealed two unique aspects of this application:
- The need to insert and remove cages from the work area (A large vertical opening was therefore provided.)
- The need for a mechanism for isolation and removal of the waste. We recently provided such a unit that is shown below which contained well under various tests: (Note the wide funnel port and wheeled-in carrier container below.)
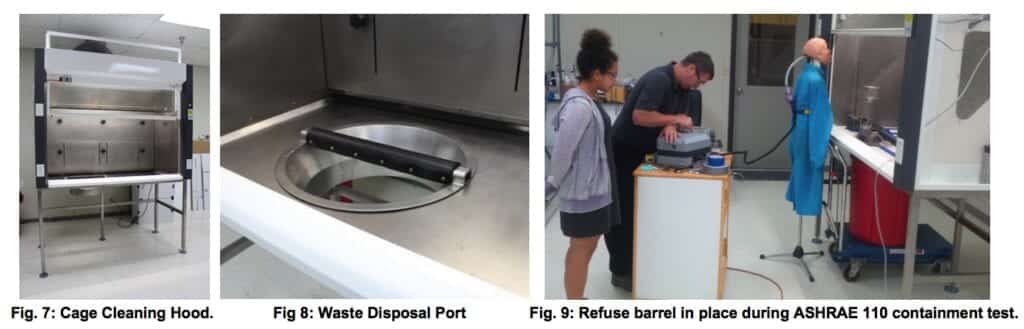
This fume hood met the process criteria of the customer and provided an easy way to isolate the waste and dispose of it while minimizing waste contamination issues. The stainless steel interior allows simplified cleaning regimens with strong disinfectants.
The customer received documentation of great ASHRAE 1101, Human as Mannequin2, and low face velocity containment results for this unit. This hood became one more tested and proven solution for animal cage cleaning Flow Sciences can offer customers!
Case 4: Hazardous chemicals requiring interconnecting hoods with pass-through features
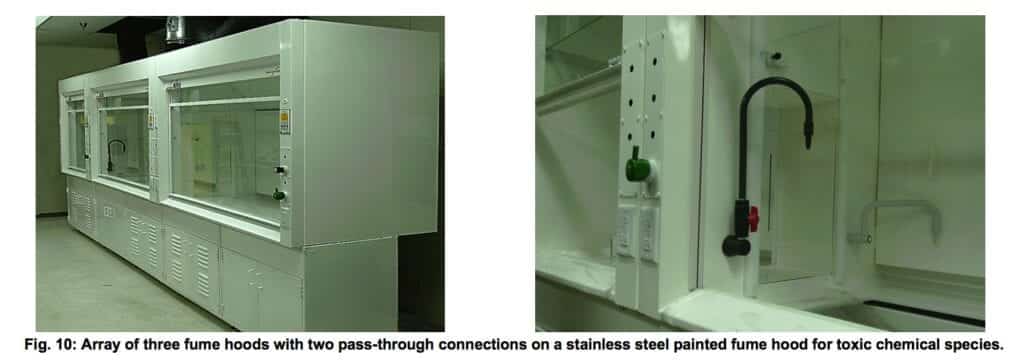
This particular fume hood almost appeared to be an exception to “listening to a customer” because it started with Flow Sciences receiving a detailed, written specification and limited ability to discuss the specification with the customer. The conditions of the quotation specified this condition.
We were able, however, to answer many of the seven questions by “asking” the specification.
We knew, for instance, the fume hood dimensions (question 2). We knew this particular fume hood array was to be used to analyze several caustic substances never to be removed from the hoods during analysis (question 1).Electrical outlets and voltages were called out (questions 4 & 5). We were also told in the specification which services were to be provided and where they were to be placed (indirectly, question 1). We were even given a paint vendor to use and which color was to be provided (again, a strong question 1 indicator). The construction contact was listed in the specification (questions 6 & 7).
While not ideal, this way of quoting and eventually testing a containment device represents a scenario which is encountered frequently. There are three things which the manufacturer can do when direct customer contact is not possible:
- When no humans are present, “ask” the specification! Any relevant specification detail should be used to justify the eventual product design.
- Be certain a detailed sign-off drawing is approved before unit construction begins.
- Test, test, test! Assume containment is critical and include standard containment tests plus movement of hood internals and manipulative tests such as the Human-As-Mannequin (HAM) test.
ASHRAE 110 and the HAM containment tests were run with excellent results. (Figs. 11-13)
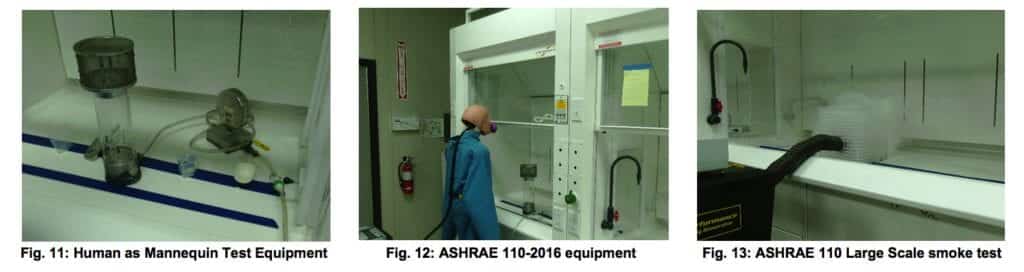
There are obvious shortcomings when manufacturers and customers do not or cannot directly talk to each other. The manufactured product will reflect an anticipated, rather than a spoken need. Changes from original research intent to what is needed at the time of purchase order approval are not possible. Back-charges, change orders, and delays during the installation process all become more likely. In spite of these things, some positive results can still be achieved largely based on the ability of the specification to “answer” key questions.
Conclusions:
This white paper began with a discussion about how communication is necessary for complex containment solutions to be reached between a research entity and an equipment manufacturer. The first three examples in this paper show effectively how such containment challenges rarely involve a catalog of equipment or a pre-written job specification. The last example demonstrates how success can still be achieved if the specification is used as a basis of assessing product requirements.
Still, the best guarantor of success is direct communication. People must talk to each other about specific applications and containment requirements. Once such a conversation has occurred, a substantive containment approach may be confidently agreed upon. Such an agreement must include enough information to let the customer visualize how this product will facilitate the application.
Problem-solvers clearly must be involved on both sides of such an interaction! Several key steps must take place before any complex containment issue can be sorted:
1) The customer’s application must be stated by the customer and acknowledged by the manufacturer.
2) A modified containment device must then be proposed.
3) This device must be constructed based on sign-off drawings approved by the customer. This device must be shown to work with the application using recognized test procedures which sometimes may require modification.
If all of the above goes well, both the customer and the manufacturer benefit!
Footnotes:
- ASHRAE 110-2016 – Methods of Testing Performance of Laboratory Fume Hoods, American Society of Heating, Refrigeration, and Air-Conditioning Engineers, 2016.
- Side-by-Side Fume Hood Test Using ASHRAE 110 and “Human as Mannequin” to Compare Performance of a Jamestown Conventional Fume Hood and a LBNL High Performance Hood, Lawrence Berkeley National Laboratory, California Energy Commission; March 21, 2005.