Analytical Process Isolator™
Continuous Process Isolator for Virus Screening &
HPAPI Handling
Our Analytical Process Isolator (API series) provides a dual containment enclosure that essentially merges our Glovebox Workstation with our VBE. We did this to offer a uni-directional flow for highly toxic processes. Material enters through the pass-thru door and moves into the glovebox where the operation takes place. The VBE section allows for a secondary wipe-down of material containers or equipment before removing it from the enclosure.
Process
The glovebox side can contain ISO 5 processes, while the VBE section allows a secondary cleaning station before removing equipment or material containers.
Containment
Third-party surrogate powder test shows exposure levels below 10ng/m3, even with large spills, dependent on quantity/potency*.
Design
The glovebox provides proper containment for most lab equipment, including balances, ovens, and sieves.
Benefits
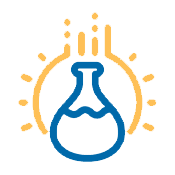
Applications
This unit excels in various applications. Designed for HPAPI/API processes. Provides containment to nanogram levels based on potency.
HEPA Filtration
Equipped with a 4” HEPA inlet and dual filtration. Creates an environment exceeding ISO 5 standards. Air can be recirculated or vented out.
Structural Materials
Constructed with a polypropylene superstructure. Features a phenolic, resin-coated base. Viewing ports in acrylic or glass.
Cleaning Station (VBE)
An open-faced environment for decontamination. Ideal for cleaning material containers. Ensures safety before complete removal.
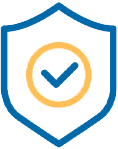
ISO 5 Interior Workspace
Top-mounted HEPA filter ensures cleanliness. Interior meets or exceeds ISO 5 standards. Provides an optimal environment for work.
Standard Sizes
Available in widths of 5′, 6′, and 7′. Units have a depth of 36” and a height of 24″. Custom dimensions are available based on need.
Useful Videos
Additional Resources
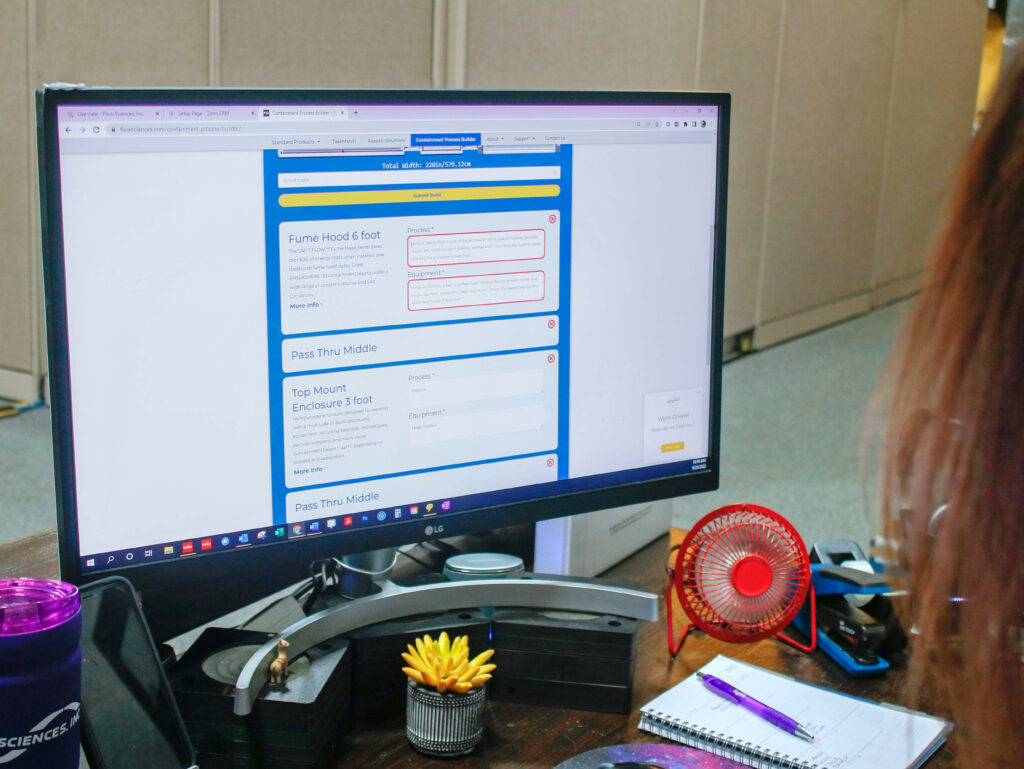
Over the years, we built an inventory of unique enclosures engineered to handle specific tasks. To offer you a better experience we have gathered these enclosures on one page. Simply search by the task or equipment to find matching enclosures.
SEARCH CONTAINMENT BY APPLICATION
Over the years, we built an inventory of unique enclosures engineered to handle specific tasks. To offer you a better experience we have gathered these enclosures on one page. Simply search by the task or equipment to find matching enclosures.
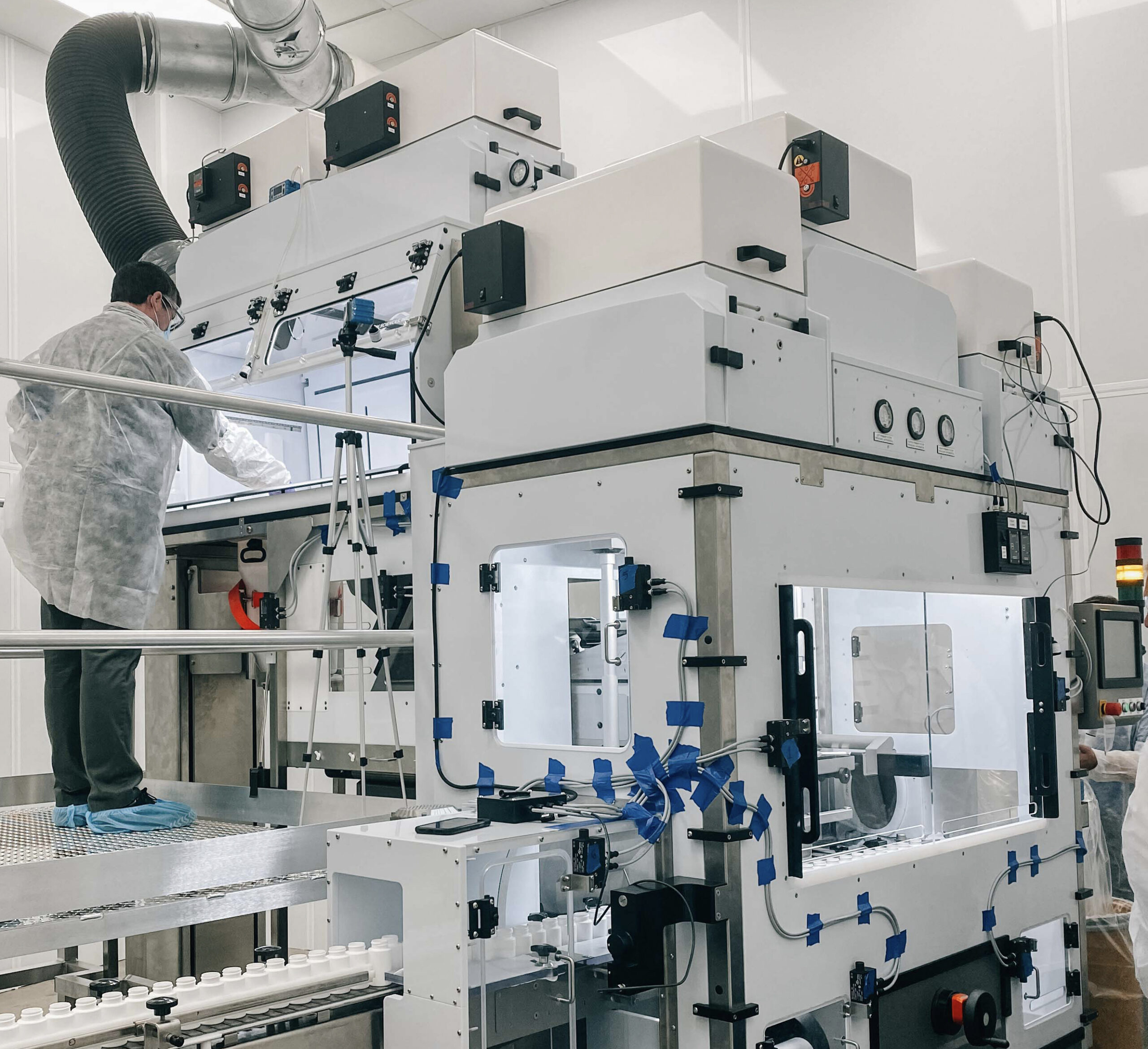
Process
Allows for ISO 5 processing and intake/outtake through a negative pressure cabinet.
Containment
Surrogate powder test results show containment below 10 ng/m3, even with large spills.
Design
The chamber on the right is a vented balance enclosure (VBE) for decontamination & cleaning.
ISO 5 Cleanliness for API Processing
Safety
The Analytical Process Isolator (API series) provides a higher level of containment than an open faced enclosure for highly toxic APIs. FSI engineered controls assist in the prevention of containment loss. Third–party testing has proven containmen to below 10 ng/m³, based on process and quantity.
ISO 5 Interior Cleanliness
The side mounted HEPA filter inlet creates a clean interior working environment that meets or exceeds ISO 5 for clean processing work.
Design
This unit is able to effectively contain API processing using a HEPA filtration system to let air in and out. The two dual stack HEPA filters can be recirculated into the lab or vented out through building exhaust.
Cleaning Station
A secondary open faced environment allows for decontamination of equipment as it enters and leaves containment.
Construction
This unit comes standard with a polypropylene superstructure and a dished base coated in phenolic resin. Viewing ports are available in acrylic (ECP Series) or glass (ECG Series).
LED Light
This enclosure features an internal, adjustable, white LED light for improved visibility. Also available in Amber LED.
HEPA Filtration
The Analytical Process Isolator is equipped with a 4” inlet HEPA filter and 2 primary and 2 secondary 4” HEPA filters that can be recirculated into the lab or sent directly to house exhaust.
STANDARD SIZES
Available in 5’, 6’ and 7’ foot standard width options. All units are 36” deep and 24” of internal height. Custom sizes available.
Question or need a quote?
Contact us using our online form, live chat, or call 1-800-849-3429. We're here to help you find the solution you need.
Contact Our Experts
SEARCH CONTAINMENT BY APPLICATION
Build Options
Product Type | Style | Material | Ext. Width | Ext. Depth | Internal Height | Base | Exhaust / Filtration | Voltage / Filter / Alarm | Options |
---|---|---|---|---|---|---|---|---|---|
E – Enclosure | C – Dual Containment | P – Poly (Acrylic viewing panels) | 60" | 36" | 24" | A – Standard | B – Fan/BIBO | D – 110-120v 50-60 Hz/ HEPA Filter/ Integrated Alarm | 0 – Pass thru left, Open face right |
G – Poly (Glass viewing panels) | 72" | E – 4" Tri-Clover Male | G – Mesh Fan/ BIBO | F – 220-240v 50-60 Hz/ HEPA Filter/ Integrated Alarm | 1 – Open Face Left, Pass Thru Right | ||||
84”" | F – No Base (Must be purchased separately) |
I–110-120v 50-60 Hz/ ULPA Filter/ Integrated Alarm |
|||||||
J – 220-240v 50-60 Hz/ ULPA Filter/ Integrated Alarm |
Accessories
Add-Ons | ||
---|---|---|
Berkshire Cleaning Kit | Contact Flow Sciences for kit description |
![]() |