Dr. Robert Haugen, Flow Sciences Inc.
Abstract:
The use of weighing equipment in all chemical and pharmaceutical endeavors is critical. In chemical research, the accurate measurement of a reaction product may directly lead to its chemical formula. In pharmacy, dry weight of a drug becomes central to administering proper dosage. Examples of the criticality of weight measurement are virtually endless!
Because Flow Sciences produces containment equipment for chemical and pharmaceutical applications, the writer will examine the impacts of weighing errors within laboratory containment devices. A review of such errors reveals that most relate to faulty equipment, unanticipated environmental factors, and negligent balance operation.
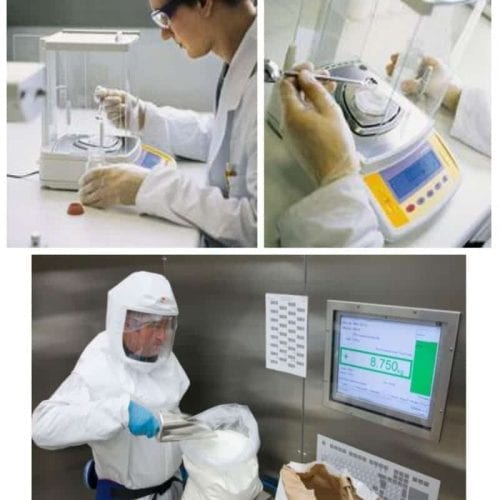
Impediments to Accuracy:
Five key impediments to accurate weighing will be detailed in this paper.
1) Vibration Interference caused by grinders, pumps, or crushing equipment can cause balance values to cycle over some midpoint. Such cycling expands the uncertainty of measurement. Many successful versions of weighing tables can minimize this issue by increasing the mass of the surface upon which the balance is placed. Increasing the table mass means the vibration energy trying to wiggle the balance is absorbed by the extra mass of the table top. Such a phenomenon is frequently called dampening.
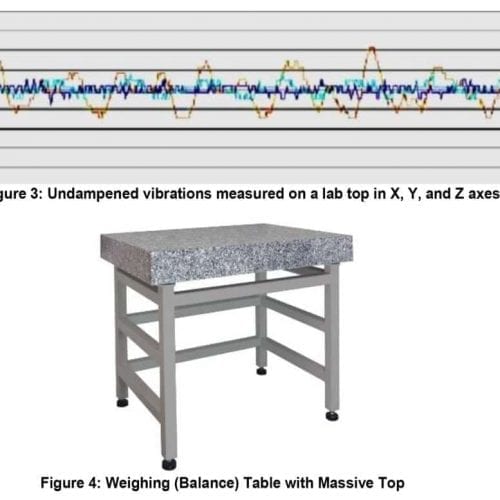
Such vibration is also common in poorly designed ventilated balance enclosures.1 Frequently, such enclosures have inexpensive fan motors poorly insulated from vibrating the weighing chamber work top. Some filtered weighing stations must be turned off before balances inside work properly. This technique is clearly not advocated by the author. The Flow Sciences weighing station pictured below features a balanced fan wheel and vibration isolation between the fan and weighing area 1.
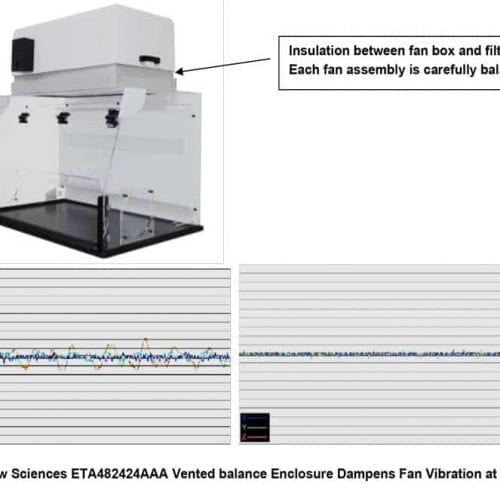
2) Instability of Chemicals being weighed: When weighing a substance that is sensitive to relative humidity, the measurement may unexpectedly increase while on the balance.
In this scenario, airborne water vapor may begin to react with the substance while it is still on the scale.
A remarkable “weight gaining” example is the slow saturation of anhydrous Copper (II) Sulfate. If left on a scale in a humid environment, this white powder will gradually turn to blue while remaining crystalline. As it is turning blue, it is also gaining ~56% more weight by absorbing water vapor!
CuSO4 + 5 H2O –> CuSO4(H2O)5
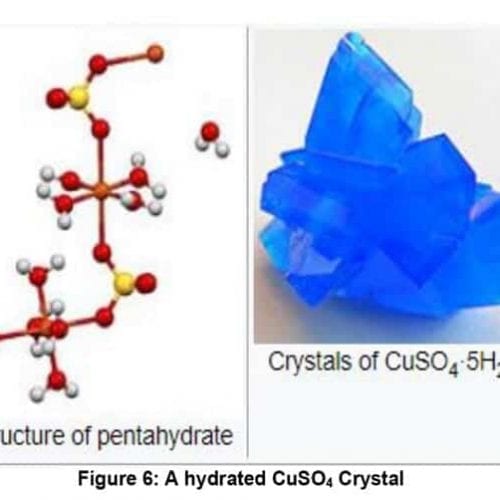
While the illustrated molecular hydrated structure shown above is not pretty, when repeated thousands of times in 3-space, it is systematic enough to form regular crystals! If such crystals are heated, they will turn white as they lose their waters of hydration.
In general, many anhydrous compounds have some potential to hydrate in ways similar to the example above. Because water vapor is so plentiful in our atmosphere, the effect of humid air on weighing anhydrous powders is pernicious. If dehydration during weighing cannot be completely solved by dehumidification of the lab, water in the weighing environment can be essentially eliminated by replacing the air in our weighing environment with a pure, unreactive gas like nitrogen or argon. The Flow Sciences NitrogenemaTM Series shown below does this with great effectiveness. Such a non-reactive atmosphere can also be used to prevent oxidation of unstable metallic compounds.2 Weighing becomes much more stable in such an environment.
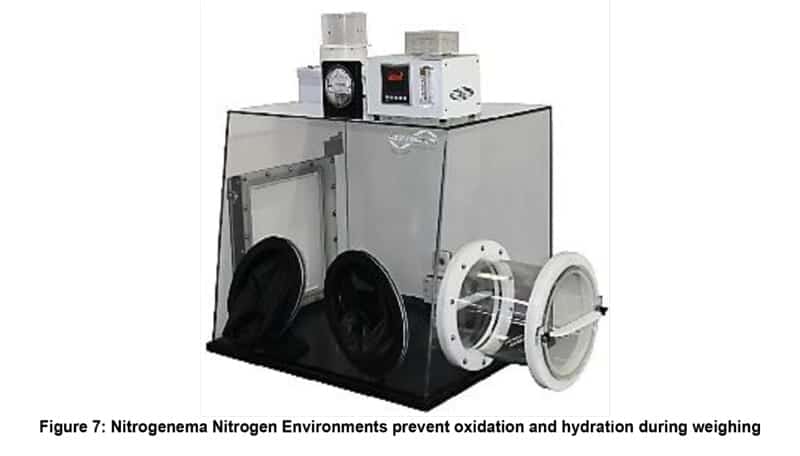
3) Air Currents: Any quick, brisk gust of air that rushes through a routinely opened sash can challenge balance stability. This type of air draft can interfere with balance measurements by blowing powdered product off the balance pan or by aerodynamically lifting, then dropping, the pan itself. This effect can be minimized by closing the door of an analytical balance, using a draft shield (photo 2 on title page), or by moving the entire weighing apparatus away from room drafts.
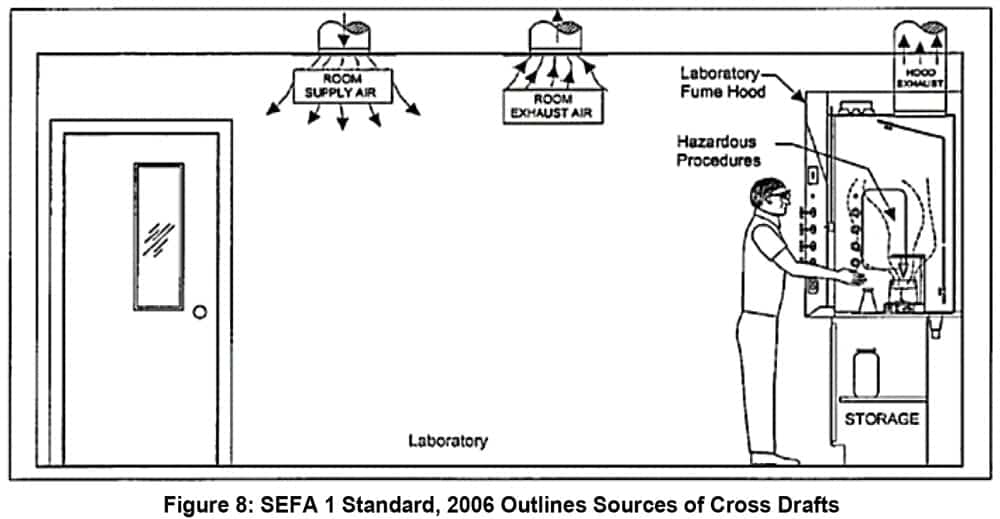
In the containment industry, these drafts in front of an enclosure are commonly referred to as “cross drafts”. Cross drafts higher than 15 linear feet per minute will cause some face velocity variations. These variations can induce weighing error, particularly with platform balances. While any properly built ventilated weighing device with stable interior velocity profiles can routinely produce stable weighing data, proximity of such an enclosure to doorways, walkways, fans, windows or make-up air vents should be avoided at all costs.
4) Temperature Variations: When samples are introduced into a microbalance environment, there may be a temperature difference between the sample and the air surrounding the sample. Such a difference can introduce convective air flow around the object being weighed. Particularly when nanogram accuracy is required, samples being weighed should be close to ambient temperature for stable and reproducible readings.
5) Ignoring sample spillage: Leaving sample residue inside a contained weighing area is a preventable way of introducing major errors into weighing. Particles smaller than 0.1 millimeters (mm) are difficult to see. Many Contract Manufacturing Organizations and Contract Research Organizations work with substances that are on the micrometer scale, which is one one- hundredth of the particle referenced above. For powders this fine, it is quite necessary to clean areas where weighing takes place even if no residue is visible! Frequent cleaning is the only way to prevent increasing measurement error in repetitive procedures. Even though what is being removed may be invisible, SOP’s should be developed to prevent balance build-up and contamination from previous procedures.
Conclusions:
As stated in our abstract, weighing errors are primarily caused by faulty equipment, unanticipated environmental factors, and negligent balance operation. Ventilated enclosures that house weighing devices should have balanced exhaust fans and a massive enough work top to yield low vibration levels necessary for stable measurements. Most manufacturers should have test data revealing this type of performance1. Remember also that balances should be recalibrated and the calibrations memorialized on a regular basis.
Several environmental factors can cause weighing inaccuracy, including humid air, dirty air, and large cross drafts. Areas with balance enclosures should always be in low traffic areas with clean air. In some cases, a chamber with a non-reactive atmosphere may be required.
Human behavior can be responsible for many measurement accuracy issues. The scale area should be kept scrupulously clean. With microgram or nanogram quantities, areas may need to be cleaned even if spillage is not visible. Flow Sciences has a video using ultra violet light that demonstrates this.
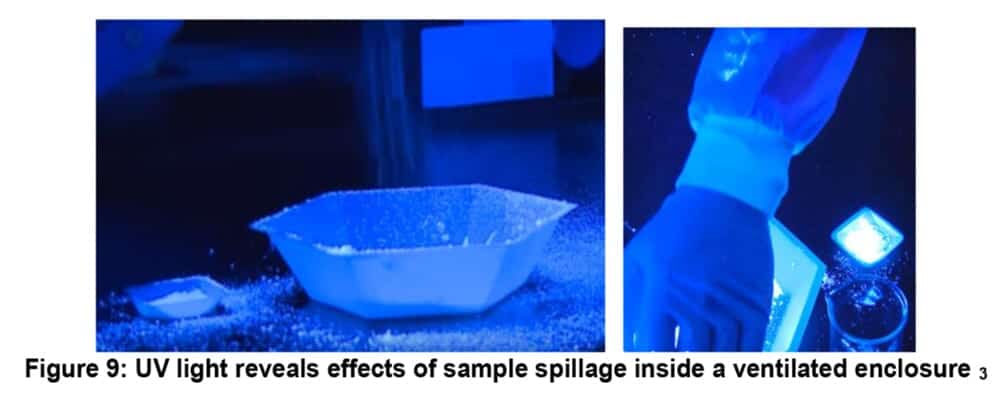
Good data keeping and memorialization are also critical and guarantee that there will always be a protected data record to back up your lab’s findings!
Footnotes:
- The Importance of Vibration Isolation for Proper Enclosure Functioning, 2016, Robert Haugen, Flow Sciences Publication
- Containment Using a Non-Reactive Atmosphere, 2019, Robert Haugen & Gary Dean, Flow Sciences Publication
- Surrogate Fume Hood Test, 2019, PowerPoint, Flow Sciences
DR. ROBERT HAUGEN
Director of Product and Technology Development
Robert K Haugen currently designs chemical laboratory containment equipment and develops new relevant technologies for Flow Sciences Inc.in Leland, North Carolina. He has also held positions at Kewaunee Scientific, Jamestown Metal Products, and St. Charles Manufacturing in similar capacities for 31 years. Previously, he did analytical chemical work at the University of Illinois (DNA, wastewater, and crop research) and Lawrence Livermore Labs in California (nuclear weapons research).
Dr. Haugen began his career as a curriculum writer for the Illinois Office of Education, developing texts on energy, urban management, and industrial pollution topics.
He received all his degrees from the University of Illinois in Urbana-Champaign, and is currently a member of the American Society of Heating, Refrigeration, and Air Conditioning Engineers, the American Chemical Society, and the National Fire Protection Association. He has participated in the development of both ASHRAE 110-1995 and the current 2016 update.